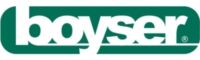
Boyser AMP-CONTROL Peristaltic Dosing Pump
Chemical Dosing Pump & Water Treatment Pump
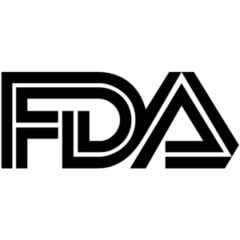
Key Specifications | |
---|---|
Max Flow Rate | 6.8lpm |
Max Head | 80M |
Max Temperature | 80ºC |
Max Viscosity | 20000 cP |
Solids | 16mm |
Size | 3/4" |
The Boyser AMP-CONTROL is an intelligent peristaltic dosing pump with integrated control functionality and variable frequency drive to allow automation, accuracy and efficiency when it comes to metering.
The main electronic functionality of this Boyser pump is that it allows preset volume or time batching to be automated at set intervals or scheduled dates/times using the intregrated calendar. This peristaltic dosing pump also comes with configurable inputs and outputs that can be used to allow external equipment signal relays to determine when the pump should operate e.g. a float switch, or for connection to external business management or process control systems e.g. Profibus.
With fluid compatibility and solid handling being limited by only the inner tube, this peristaltic pump design can accurately dose a wide variety of fluids including viscous, solid laden, shear sensitive mediums and aggressive chemicals, without risk of seals leaking and valves blocking.
Another huge benefit of the inner hose being the only wetted part is that there is only one component to wear and maintain. As a fail safe, the Boyser AMP-CONTROL peristaltic pump also comes with a hose replacement alert for preventive maintenance after a set interval based upon its built in machine learning, and a tubing rupture sensor to shutdown the pump, alert operator and allow for quick replacement should it unexpectedly fail. When maintenance of the inner tube is required, the user is guided through replacement on the digital screen meaning onsite personnel can carry this out.
The Boyser AMP is a roller operated peristaltic hose pump as opposed to being shoe operated. As less friction is generated with this design, the user benefits from lower power consumption, a lower starting torque which gives a smoother operation and makes it easier to adjust speed, and also easier hose maintenance as it doesn’t require lubrication.
Features of the AMP peristaltic hose pump:
- Inverter driven for speed and output control
- 3" digital screen control panel with display in 12 languages
- Direct reading of the flow rate on the digital display
- Batch function for preset volume or time metering at set intervals or scheduled dates/times
- Integrated calendar for automatic start/stop by date and time
- Input and outputs for operation of pump by external signal relays
- Has 4-20ma and BUS outputs for connection to external BMS or process control systems e.g. Profibus
- Hose replacement alert for preventative maintenance
- Tube rupture/leak sensor to shutdown the pump and alert the operator immediate replacement is required
- Good suction lift and self priming up to 8 metres
- Can dry run without damage and handle viscous and solid laden fluids
- Inner hose available in a variety of materials for compatibility with almost any fluid.
- Seal-less design makes them less likely to leak – ideal for chemicals and aggressive fluids
- Gentle pumping motion and low rpm for handling shear sensitive fluids
- Reversible operation allowing tank to tank transfer and the recovering of fluid from the dispensing hose if required at the end of transfer
- Patented double conical hose clamp to ensure leak free connection
- Heavy duty internal ball bearing box that means the motor and gear reducer shaft do not have to support of all of the load, adding strength and increasing life span
- Wrapped inner and outer hose, reinforced with high density pressed Nylon for longer life
- Simple and lost cost to maintain thanks to the hose being the only wearing part, which is easy to clean and replace, and the absence of valves and seals that can clog and wear.
- 100v-230v, 50hz / 60hz motors available
FAQs
Peristaltic pumps are part of the rotary positive displacement pump family. They are made up of just two components; a rotor that has a number of rollers or a "shoe" attached and a flexible internal hose/tube fitted inside a circular pump casing. As the rotor turns, the attached rollers compress the tube where the fluid is contained, and that continuous motion forces the liquid from the pump's inlet to its outlet.