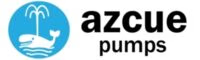
Azcue KL Progressive Cavity Pump
Abrasive Solids & Viscous Fluid Pump
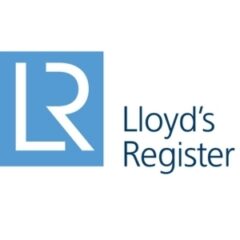
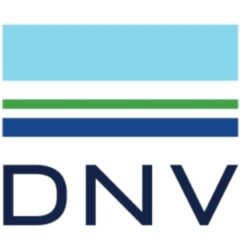
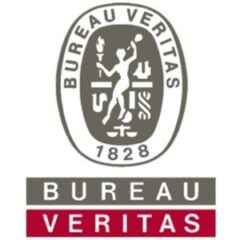
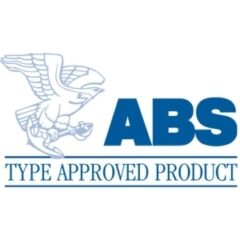
Key Specifications | |
---|---|
Max Flow Rate | 560M³H |
Max Head | 480M |
Max Temperature | 140 °C |
Max Viscosity | 200,000 cP |
Solids | 150mm |
Size | DN20 to DN100 |
The Azcue KL Progressive Cavity Pump is a large, robustly constructed solution designed for harsh pumping conditions thanks to their ability to handle difficult fluids even over long distances thanks to the high pressures they can achieve. The low internal velocity design of the eccentric screw pump means that the KL can transfer extremely viscous fluids containing solids effectively such as sewage and slurries, as well as shear sensitive fluids than need to maintain their structure during the pumping process.
With higher flow and higher solids handling capabilities (up to 150mm) than the KB, the KL progressing cavity pump is the ideal option for more heavy duty applications where larger volumes of fluid need to be transferred or the media has particularly large and abrasive contaminants.
Whilst being closed coupled, the Azcue KL helical rotor pump has a bearing bracket which is coupled to the motor via a plug connection which is easy to service and relieves the strain on the shaft and gears, making them suitable for continuous application. This bracket also means that there is still space between the pump and motor so in the case of seals wearing out, water leaked from the pump head would not enter the motor.
Other design benefits of the KL Azcue pump is its fully encapsulated cardan shaft and joint as standard with lifetime lubricated needle roller bearings that are wear and maintenance free. Its joint connections, which have equivalent diameters, ensure a constant flow within the suction housing to prevent blockages in the pump.
For more information on the working principle and applications for which progressive cavity pumps are most suited, read our guide.
Features of the Azcue KL Progressing Cavity Pump:
- High pressure progressing cavity pump
- Self priming to handle difficult suction conditions
- Enables the free passage of solids up to 150mm
- Max viscosity of 200,000 mPas
- Bearing bracket between pump head and motor to share strain
- Lifetime lubricated roller bearings
- Equivalent diameter joint connections to prevent blockages
- Low pulsation, continuous flow
- Suction housing with large inspection and clean openings
- Easy to replace cartridge format seal package
- Available in cast iron or stainless steel
- Electric or hydraulic motor driven
- Optional hopper feed or base plate
FAQs
It consists of a spiralled helical rotor (like a cork screw) that sits tightly inside a rubber stator/sleeve. As the rotor turns inside the stator, it forms a set of fixed-shaped cavities that progress along the length of the stator and force the fluid inside to move along with them as they turn.