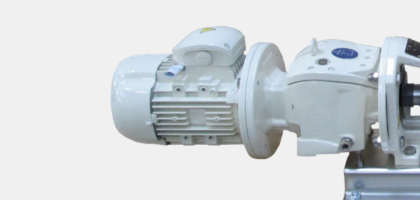
Progressive Cavity Drum Pumps
Need help specifying the right progressive cavity pump? Contact our pump experts today!
8 products
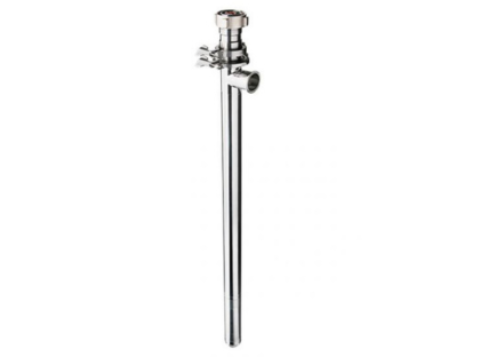
- Max Flow Rate: 80lpm
- Max Head: 150M
- Max Temperature: 100°C
- Max Viscosity: 80,000 cP
- Solids: 8mm
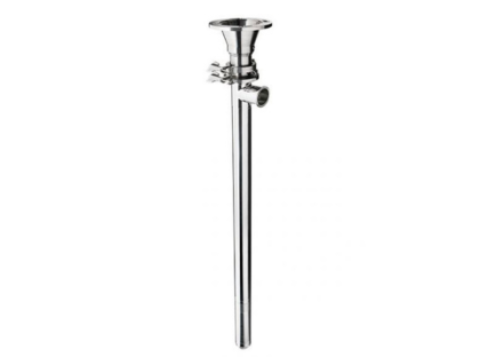
- Max Flow Rate: 80lpm
- Max Head: 150M
- Max Temperature: 100°C
- Max Viscosity: 100,000 cP
- Solids: 10mm
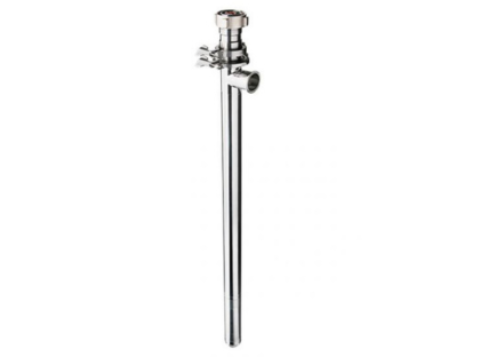
- Max Flow Rate: 80lpm
- Max Head: 150M
- Max Temperature: 100°C
- Max Viscosity: 80,000 cP
- Solids: 8mm
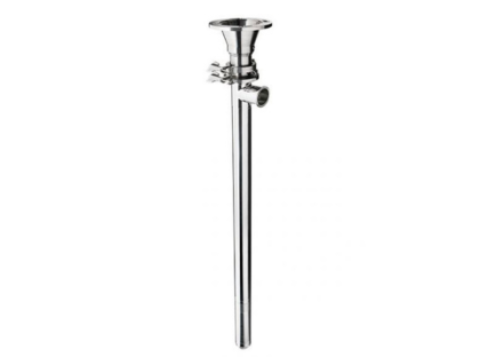
- Max Flow Rate: 80lpm
- Max Head: 150M
- Max Temperature: 100°C
- Max Viscosity: 100,000 cP
- Solids: 10mm
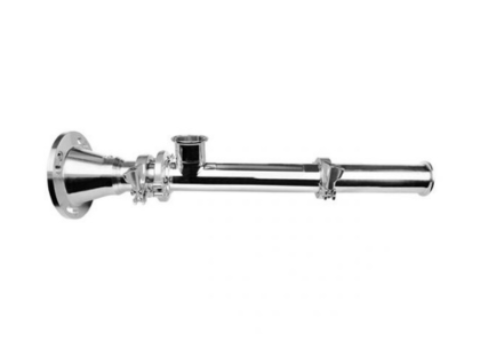
- Max Flow Rate: 80lpm
- Max Head: 15M
- Max Temperature: 100°C
- Max Viscosity: 100,000 cP
- Solids: 10mm
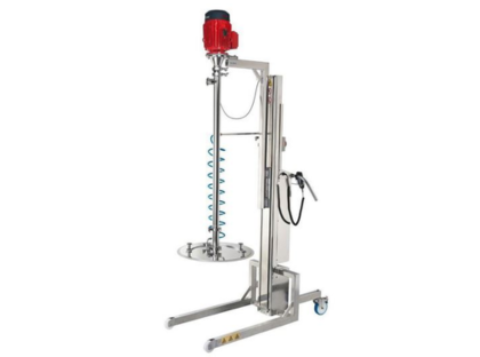
- Max Flow Rate: 50lpm
- Max Head: 80M
- Max Temperature: 120°C
- Max Viscosity: 500,000 cP
- Solids: 8mm
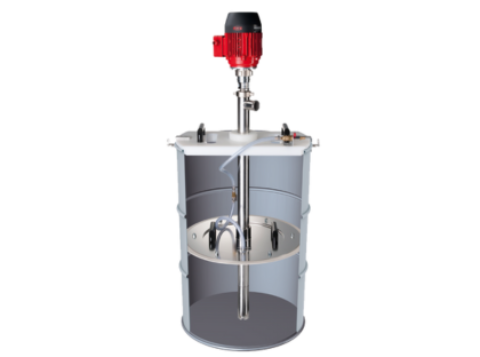
- Max Flow Rate: 50lpm
- Max Head: 80M
- Max Temperature: 120°C
- Max Viscosity: 500,000 cP
- Solids: 8mm
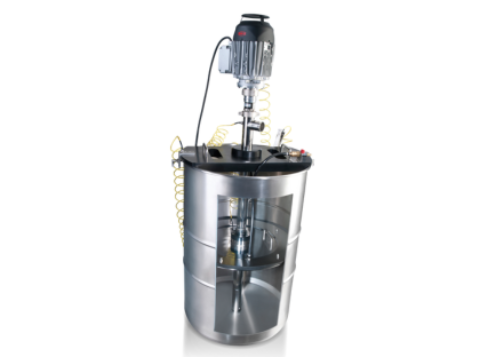
- Max Flow Rate: 30lpm
- Max Head: 80M
- Max Temperature: 120°C
- Max Viscosity: 500,000 cP
- Solids: 8mm
FAQs
No! Even short period of dry running can result in damage to the rotor and stator, making dry run protection a must if there is risk of this.