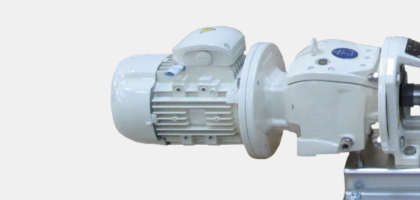
Progressive Cavity Pumps
Need help specifying the right progressive cavity pump? Contact our pump experts today!
Progressing cavity pumps for viscous fluids & slurries
Progressive cavity pumps are a type of positive displacement pump, also referred to as a helical rotor pump, a mono pump or an eccentric screw pump. Thanks to their ability to handle viscous fluids, slurries, liquids that contain large particles, gas-liquid mixtures and sheer sensitive fluids, the progressing cavity pump is a popular type of pump for potentially tough applications when other pumps may fail. Read our progressive cavity mono pump guide here.
products
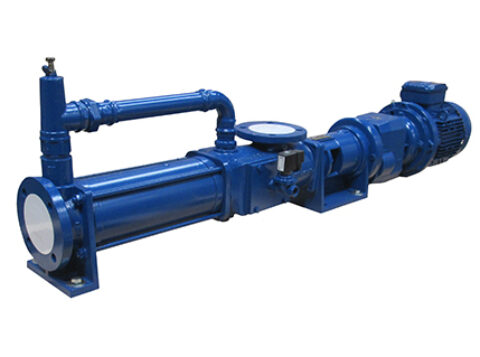
- Max Flow Rate: 560M³H
- Max Head: 480M
- Max Temperature: 140 °C
- Max Viscosity: 200,000 cP
- Solids: 150mm
- Size: DN20 to DN100
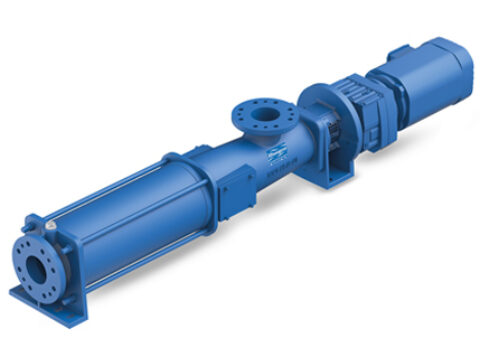
- Max Flow Rate: 147M³H
- Max Head: 480M
- Max Temperature: 140°C
- Max Viscosity: 200,000 cP
- Solids: 95mm
- Size: DN20 to DN50
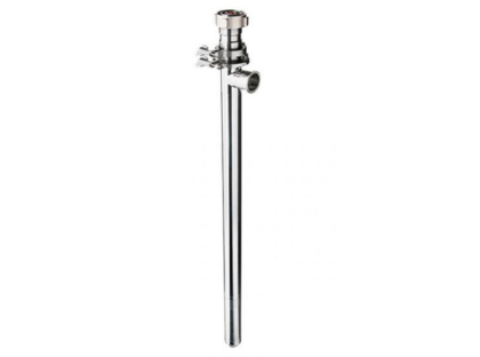
- Max Flow Rate: 80lpm
- Max Head: 150M
- Max Temperature: 100°C
- Max Viscosity: 80,000 cP
- Solids: 8mm
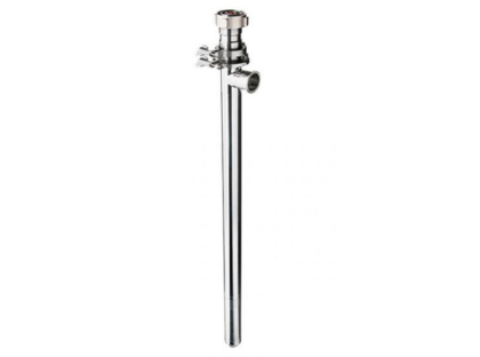
- Max Flow Rate: 80lpm
- Max Head: 150M
- Max Temperature: 100°C
- Max Viscosity: 80,000 cP
- Solids: 8mm
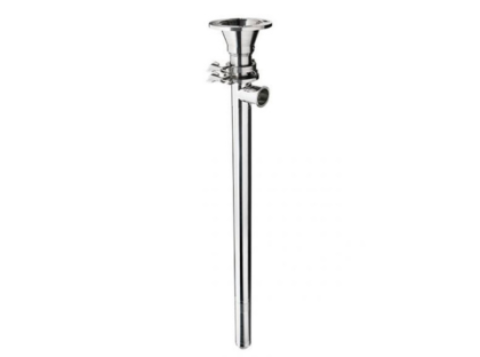
- Max Flow Rate: 80lpm
- Max Head: 150M
- Max Temperature: 100°C
- Max Viscosity: 100,000 cP
- Solids: 10mm
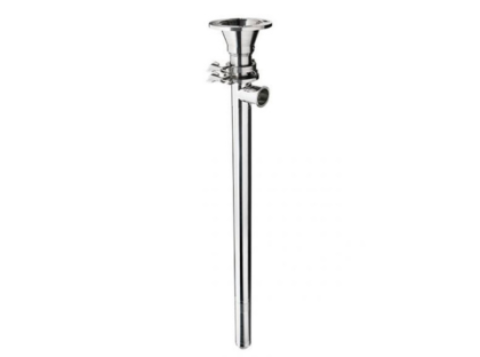
- Max Flow Rate: 80lpm
- Max Head: 15M
- Max Temperature: 100°C
- Max Viscosity: 100,000 cP
- Solids: 10mm
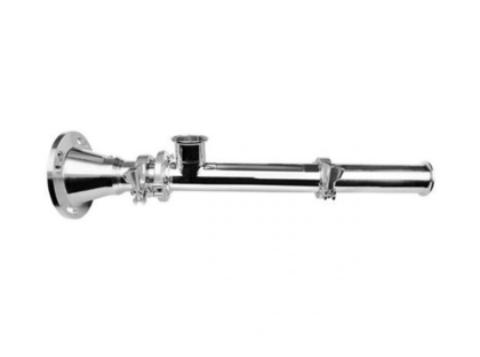
- Max Flow Rate: 80lpm
- Max Head: 15M
- Max Temperature: 100°C
- Max Viscosity: 100,000 cP
- Solids: 10mm
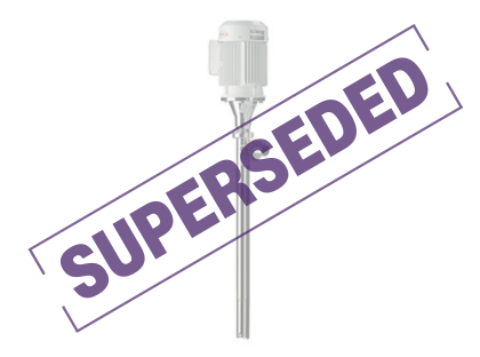
- Max Flow Rate: 50lpm
- Max Head: 80M
- Max Temperature: 120°C
- Max Viscosity: 80,000 cP
- Solids: 10mm
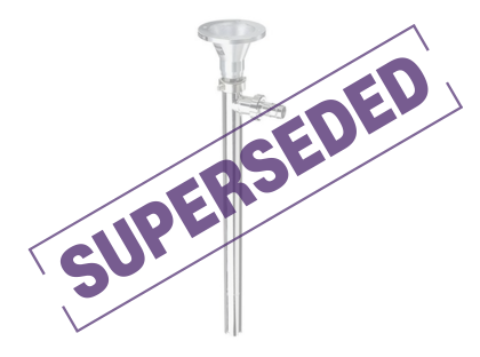
- Max Flow Rate: 50lpm
- Max Head: 80M
- Max Temperature: 120°C
- Max. Viscosity: 80,000 CP
- Solids: 10mm
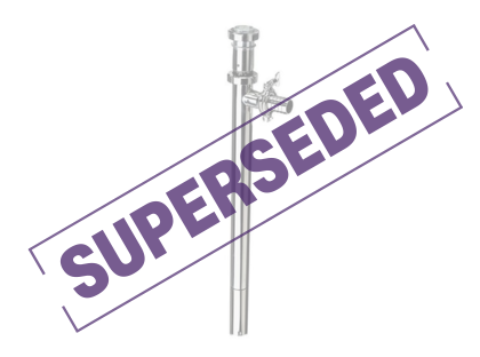
- Max Flow Rate: 50lpm
- Max Head: 80M
- Max Temperature: 120°C
- Max Viscosity: 30,000 cP
- Solids: 8mm
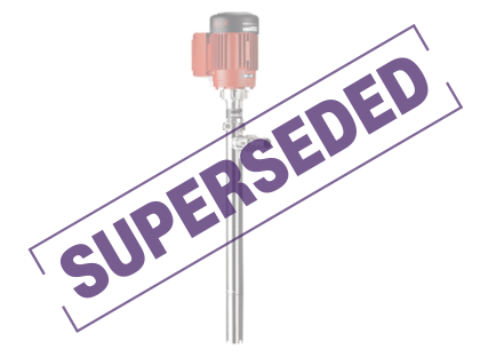
- Max Flow Rate: 20lpm
- Max Head: 80M
- Max Temperature: 120°C
- Max Viscosity: 80,000 cP
- Solids: 10mm
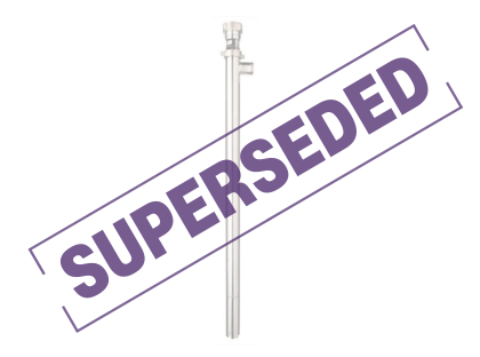
- Max Flow Rate: 50lpm
- Max Head: 80M
- Max Temperature: 120°C
- Max Viscosity: 30,000 cP
- Solids: 8mm
FAQs
It consists of a spiralled helical rotor (like a cork screw) that sits tightly inside a rubber stator/sleeve. As the rotor turns inside the stator, it forms a set of fixed-shaped cavities that progress along the length of the stator and force the fluid inside to move along with them as they turn.
Their pressure capabilities and viscosity handling is unrivalled, which means that whilst they are quite expensive in design and large in footprint, they are often selected for applications when all other pumping technologies will fail.
The design is best suited to highly viscous and lubricating fluids including oils, sludges, waste matter, biomass, pastes and grape pressing that may contain very large solids, as well as pumping viscous products over long distances.
Yes! A progressive cavity pump's tight tolerances mean it has excellent suction capabilities.
Yes! However, it should be noted that abrasive fluids e.g. low viscosity/water based fluids containing solids may cause shorter stator wear. Therefore whilst large solids and high solid content can be handled, this is usually reserved for viscous, lubricating fluids.
Our progressing cavity pumps can be supplied with auger feed allowing non-flowing mediums such as dry sludge and waste matter to be pumped without clogging. We can also provide liquid injection ports which are popular when liquid waste is added to dry content waste to allow it to flow.
No! Even short period of dry running can result in damange to the rotor and stator, making dry run protection a must if there is risk of this.