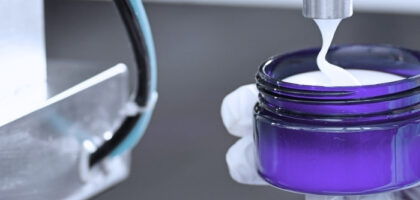
Progressive Cavity Dosing Pumps
Discuss your dosing or metering application with our pump experts today!
Progressive Cavity Metering Pumps for Accurate Dosing
For over 10 years, Castle Pumps have been supplying pumping solution to the industrial and marine market, meaning we have extensive product knowledge and experience and can help you select the right pump for your application. Our range of progressive cavity metering pumps includes robust, high quality pumping solutions design for handling viscous fluids, slurries, liquids that contain large particles, gas-liquid mixtures and shear sensitive fluids, which makes our progressing cavity dosing pumps a popular choice for potentially tough applications when other pumps may fail. As progressive cavity pumps can provide the same flow rate regardless of the viscosity of the fluid being pumped, they are an ideal solution for when a constant flow for dosing is required, but the thickness of the fluid may be variable. So if you are searching for a heavy duty pumping for dosing viscous fluids, our progressive cavity pumps are probably the right pump for your application. Contact our technical sales engineers today for advice in selecting the right model.
products
FAQs
A dosing pump, otherwise known as a metering pump, is designed to very precisely deliver a specific quanitity of fluid to a container, tank or fluid stream at controlled intervals.
Dosing pumps are able to provide precise metering through their smooth, pulsation free operation and ability to achieve extremely low flow rates whilst maintaining accuracy.
Thanks to their accuracy at low flow rates and smooth pumping, peristaltic pumps, progressive cavity pumps and diaphragm pumps and lobe pumps are most commonly used in dosing systems.
Metering pumps are typically used to accurately delivery ingredients, additives and chemicals in food, process and water treatment industries.
It consists of a spiralled helical rotor (like a cork screw) that sits tightly inside a rubber stator/sleeve. As the rotor turns inside the stator, it forms a set of fixed-shaped cavities that progress along the length of the stator and force the fluid inside to move along with them as they turn.
Their pressure capabilities and viscosity handling is unrivalled, which means that whilst they are quite expensive in design and large in footprint, they are often selected for applications when all other pumping technologies will fail.
No! Even short period of dry running can result in damage to the rotor and stator, making dry run protection a must if there is risk of this.
It consists of a spiralled helical rotor (like a cork screw) that sits tightly inside a rubber stator/sleeve. As the rotor turns inside the stator, it forms a set of fixed-shaped cavities that progress along the length of the stator and force the fluid inside to move along with them as they turn.
The design is best suited to highly viscous and lubricating fluids including oils, sludges, waste matter, biomass, pastes and grape pressing that may contain very large solids, as well as pumping viscous products over long distances.