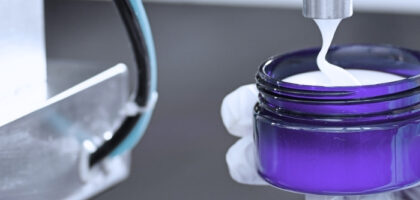
Diaphragm Dosing Pumps
Discuss your dosing or metering application with our pump experts today!
7 products
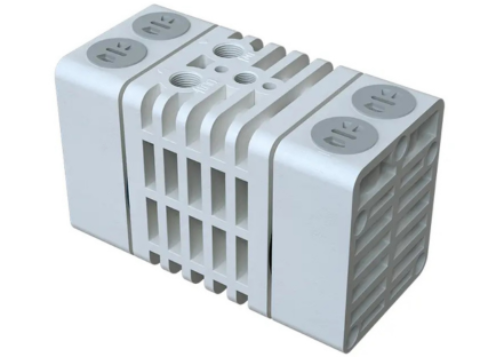
- Max Flow Rate: 6lpm
- Max Head: 80M
- Max Temperature: 95⁰C
- Max Viscosity: 800 cP
- Solids: 0mm
- Size: 1/4"
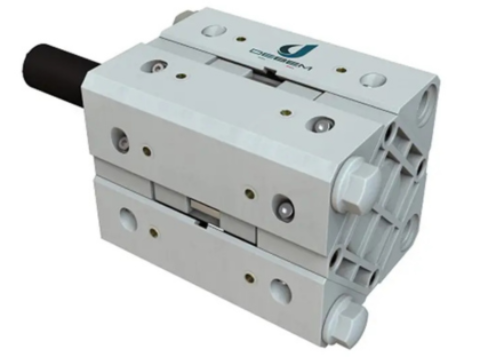
- Max Flow Rate: 17lpm
- Max Head: 80M
- Max Temperature: 95ºC
- Max Viscosity: 15000 cP
- Solids: 0.5mm
- Size: 3/8”
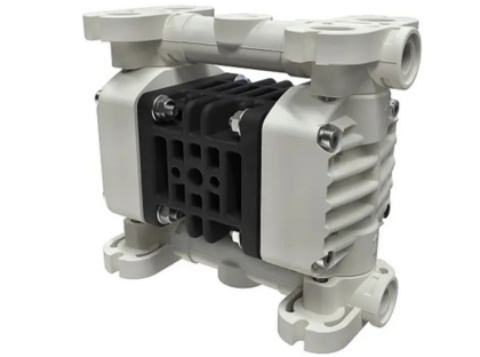
- Max Flow Rate: 9lpm
- Max Head: 80M
- Max Temperature: 95ºC
- Max Viscosity: 15000 cP
- Solids: 0.5mm
- Size: 1/4"
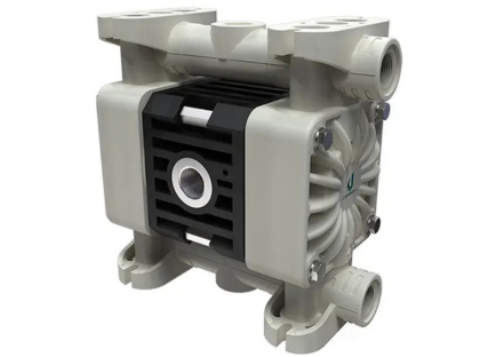
- Max Flow Rate: 17lpm
- Max Head: 80M
- Max Temperature: 95ºC
- Max Viscosity: 15000 cP
- Solids: 0.5mm
- Size: 3/8"
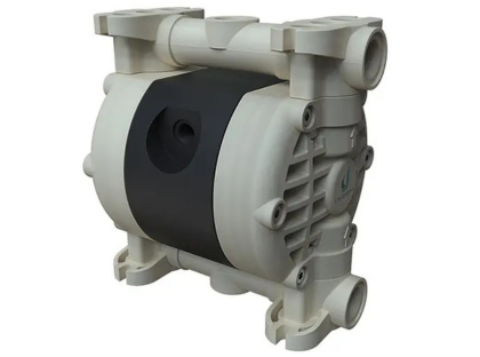
- Max Flow Rate: 35lpm
- Max Head: 80M
- Max Temperature: 95ºC
- Max Viscosity: 20000 cP
- Solids: 2mm
- Size: 1/2"
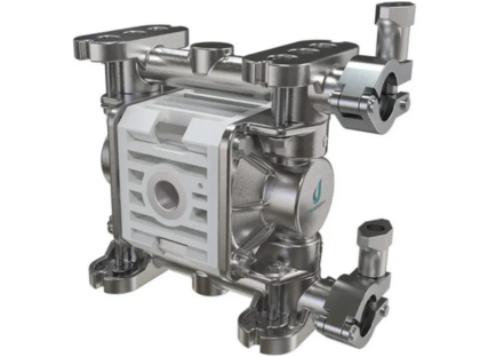
- Max Flow Rate: 17lpm
- Max Head: 80M
- Max Temperature: 95ºC
- Max Viscosity: 15000 cP
- Solids: 0.5MM
- Size: 3/4"
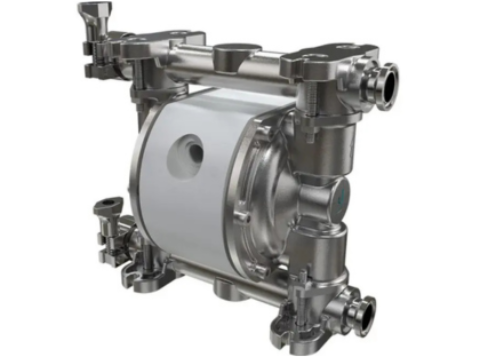
- Max Flow Rate: 35lpm
- Max Head: 80M
- Max Temperature: 95ºC
- Max Viscosity: 15000 cP
- Solids: 2mm
- Size: 1/2"
FAQs
A dosing pump, otherwise known as a metering pump, is designed to very precisely deliver a specific quanitity of fluid to a container, tank or fluid stream at controlled intervals.