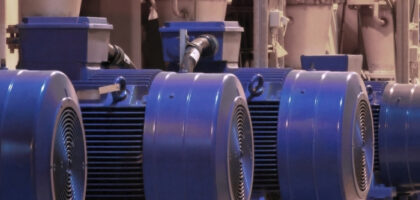
IMO 2020 Sulphur Cap Compliance
With the International Maritime Organisation's 2020 Sulphur Cap fast approaching, there are over 70,000 ship owners having to make changes to ensure they are compliant with the new 0.5% sulphur limit. There are a range of solutions available to ensure compliance from the user of low sulphur fuels to employing scrubber systems that clean the emissions of traditional HFOs. Whichever option is selected new pumping solutions are required.
IMO's 2020 Sulphur Cap
With a worldwide trend of stricter air pollution regulations and heightened environmental concern, sulphur (SOx) emissions have been a topic amongst the maritime industry for several years. After consideration of the availability of low sulphur fuels, the International Maritime Organisation (IMO) have decided that the global 0.5% sulphur cap will enter into force in 2020. These requirements are in addition to the existing 0.1% sulphur limit in place in Emission Control Areas (ECAs) in parts of Europe and North America. So, what does this mean for the industry?
According to DNV GL, the global sulphur cap affects 70,000 vessels now that stricter limits are to be enforced worldwide. With the sulphur cap deadline looming, the International Chamber of Shipping are urging shipowners to "commence implementation plans as soon as possible" to get their fuel system compliant and avoid penalties come 2020. Consequently, shipowners are now having to weigh up their options, as there isn’t a one size fits all solution…
So, what are your compliance options?
1. Low sulphur fuels
After 2020, it will no longer be permitted to carry heavy fuel oils (HFO) for feeding the engines unless scrubbers are being used (which we will come onto). Therefore, the first of the two most popular solutions to discuss is the use of low sulphur fuels. Due to the differences in viscosity, many existing systems and pumps used on board are not compatible, and therefore vessels are increasingly undergoing fuel conversions from HFO to fluids such as Marine Gas Oil (MGO). Whilst this is deemed to be a less complex compliance option, there is some uncertainty as to what the increased demand will do to the cost and availability of these fuels.
The composition of low sulphur fuels mean that they have two main differences compared to standard fuel oil; a lower viscosity and a lower lubricity. Traditionally, fuel oils used for marine engines can have viscosities up to 1000cSt, whereas low sulphur fuels are only a fraction of this. The use of existing pumps that were previously specified for higher viscosity fuels can result in leaking from the seals and connections, as well as a loss of pressure meaning that the required duty is no longer achieved. The lower lubricity level of the fluid can also result increased wear of the internal parts of some pumping technologies such as gear pumps. For that reason, marine fuel pumps now to be used with compliant fuels may need to be replaced with low sulphur fuel pumps that are able to meet the flow and pressure requirements whilst pumping a lower viscosity fuel.
2. Scrubber systems
As briefly mentioned, scrubber systems are an alternative solution that enables the continued use of HFO by removing SOx emissions from the vessel’s exhaust gases using sea water (open loop systems) or alkalis such as caustic soda (closed loop systems) to neutralise the sulphur. Both open and closed loop scrubber installations require the use of pumps to operate. The below diagram explains the difference between open and closed looped scrubber systems, and where pumps fit into them in more detail.
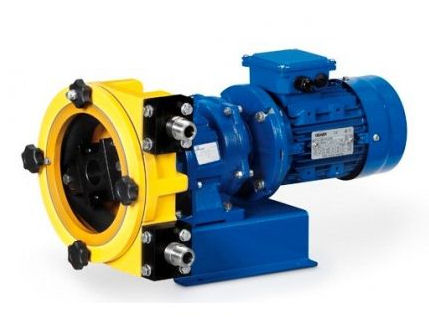
Open loop scrubbers rely on a sea water pump to transfer seawater to the scrubber. In order to accurately dose the required quantity of seawater into the system, often sea water dosing pumps for scrubbers are installed into a such a system. Closed loop systems on the other hand circulate the alkalis such as caustic soda around the system to neutralise the gases. As these pumps may be continuously run whilst the ship engine is operating, a long life, efficient design it vital.
The best solution for you
Whilst cheaper to install, operate and maintain than closed loop systems, the open loop design cannot be used in areas with restrictions on water discharge and are less reliable where sea water alkalinity it low. Whilst close loop systems can operate in all areas, they are much more complex, especially with the added costs associated with handling chemicals to consider. Overall both scrubber types are more costly, complex and require more installation room to hold the scrubber tower than the use of low sulphur fuels. In the long run however, if the price difference between low and high sulphur fuels is high then scrubbers may become more desirable than LSFO.
Both of the discussed solutions have their place; it depends upon the individual business case as to which is the better option. Castle Pumps have already helped many vessels with the specification and supply of low sulphur fuel pumps and scrubber pumps for the circulating and transfer of sea water. We welcome you to send our technical sales engineers your pump enquiries at sales@castlepumps.com or +44(0)1773 533 283.
Are you ready for 2020?
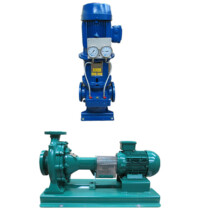
You don't have long to make sure you're compliant with the new 0.5% sulphur limit. We can help you get your pumps in order:
- Designed for fuel with as little as 0.1% sulphur content
- Smaller footprint than gear pumps for space saving
- High flow capabilities for quick transfer of bulk volumes
- Cast in bronze; shorter leadtimes & cheaper than stainless
- Long life design for even continuous running applications
- Marine type approved by classification societies