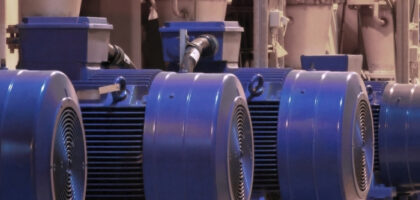
Typical Problems the Wrong Pump Can Cause Your Process
There isn’t such thing as just a pump. There are multiple different pumping technologies, and the working principle of each pump type determines its suitability to a particular application. So, when selecting a pump there are many considerations involved in getting the right one for your application. However, there are some very typical scenarios where getting the wrong pump can result in it costing you time, money or an imperfect product.
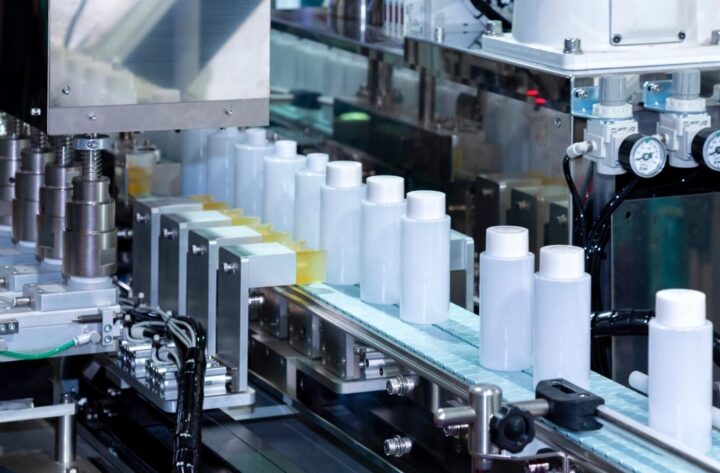
An Inconsistent Product
When you are producing chemicals, food, drink or a cosmetic product, consistency in that product is vital. Inaccuracy in transferring a liquid can result in an inconsistent product. Your customers won’t accept if a batch is different to last time without good reason about ingredients being changed, what your pump can help control is the consistent and accurate dosing of ingredients.
By using a smooth, non-pulsing flow pump with the addition of a batch meter, you can guarantee that the same quantities are added to each mixture. This is a lot more effective than relying on the human eye! Some pump types such as flexible impeller pumps and progressive cavity pumps offer a constant output without any pressure spikes, which makes them ideal for dosing applications.
Unexpected Changes in Consistency
Here the focus is on fluid shear sensitivity which refers to a fluid that changes the structure of viscosity when under force. Certain pumps apply more shear to the fluid when they operate than others such as centrifugal pumps, which can result in your fluid being altered beyond what is acceptable.
So let’s say you are pumping double cream to be packaged up and sold on. If you used a centrifugal pump to transfer this, the cream would get thicker and could even up as whipped cream, which isn’t what your customers are ordering. In this instance, it is critical that a low shear pump, positive displacement pump is selected for your application.
Clogging and Crushing Solids
When a fluid contains solids it is always important that the selected pump can handle the size solids in question without clogging or damaging the pump’s internals. For example, a fluid containing solids such as sand, oily sludge or tissue paper could result in impellers or valves blocking if the wrong pump is selected.
However, when it comes to some applications, particularly those common in the food industry, there is often another consideration when it comes to solids. It isn’t just a case of being able to move them, but also being able to do so without damaging them. For example, if you have a soup that contains meat and vegetables, you need to pieces to remain whole, not mushed into the liquid. In this instance, not only do you need a pump design capable of handling the solids, but also a low shear, positive displacement pump.
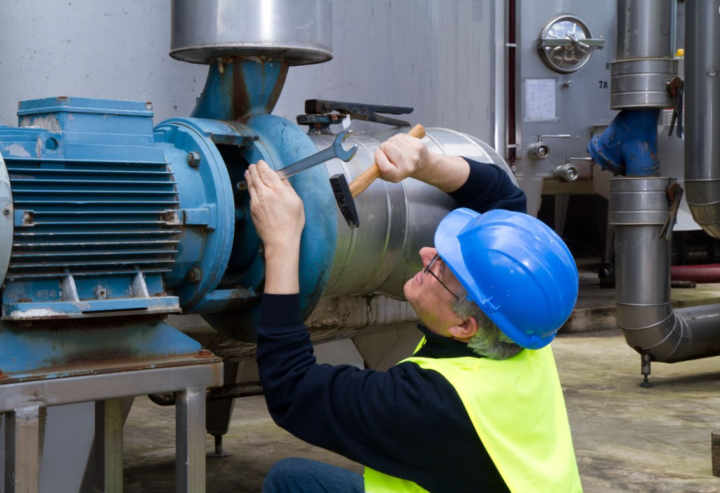
Excessive Wear
Any pump will have wearing parts that eventually need replacing, but if you’re finding that parts of your pump are wearing quickly, then this is a clue that the pump you are using may not be ideal for your process. Common issues including premature seal failure and damaged impellers could be down to several things such as fluid incompatibility, abrasives in the fluids that the pump can't handle, or excessive pressure and temperature requirements.
Pump models have maximum solid handling, operating pressure and temperatures for a reason. If these are exceeded once the pump installed, then damage to the internals can be expected. Make sure that when selecting a pump your supplier is fully aware of all of the application requirements so they can specify a fit for purpose solution.
Manual Intervention
Are your workers spending more time than necessary operating the pump? The time involved in having to walk to and from the pump to start/stop it can result in huge productivity losses. The right pump will have considered automation control features such as pump timer, dry run protection, batch meters, level switches that allow the pump to be left to do its job with as little manual intervention as possible from your operators.
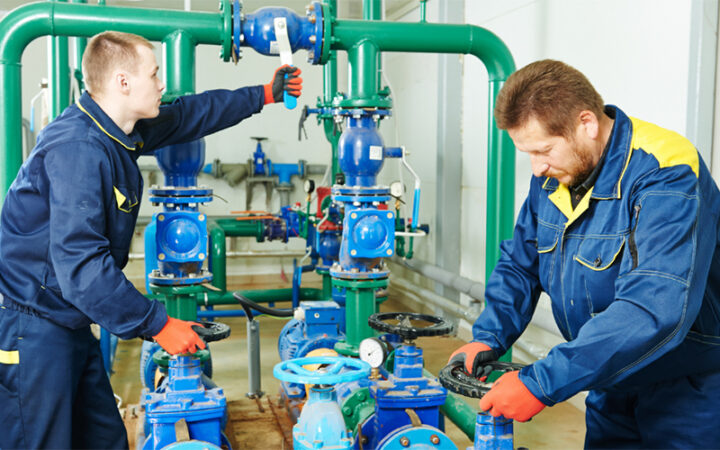
Time Consuming Cleaning
Being easy to disassemble and clean is always a benefit for any industrial process. Whether it is a chemical pump transferring harsh chemicals or a heavy-duty pump pumping cement, paint, cleaning the pump is an essential part of any industrial process. However, for food, pharmaceutical and cosmetic applications it is critical to maintain and clean the pump according to industry hygienic standards to ensure there is not any risk of bacteria growth.
Whilst pump cleaning is essential for any industry, the process can be time-consuming if it involves taken the pump out of the pipework regularly. So for applications that required more regular pump cleaning and sterilisation opting for a clean in place pump can save lots of time as the pump can undergo cleaning without having to remove it from its installation or dismantle it
Product Wastage
When dealing with expensive ingredients or hazardous liquids, any product waste can be costly and should be avoided. Many pumps struggle to completely strip or empty containers which means that a percentage of product from every container can end up being disposed of. Certain ranges, particularly of immersed barrel pumps with long down tubes are able to empty up to 99.98% of a drum or IBC preventing this.
Another example of where waste can be incurred is if the absence of batch meters or control features on the pump results in too much of a product being transferred that then has to be disposed of without being used.
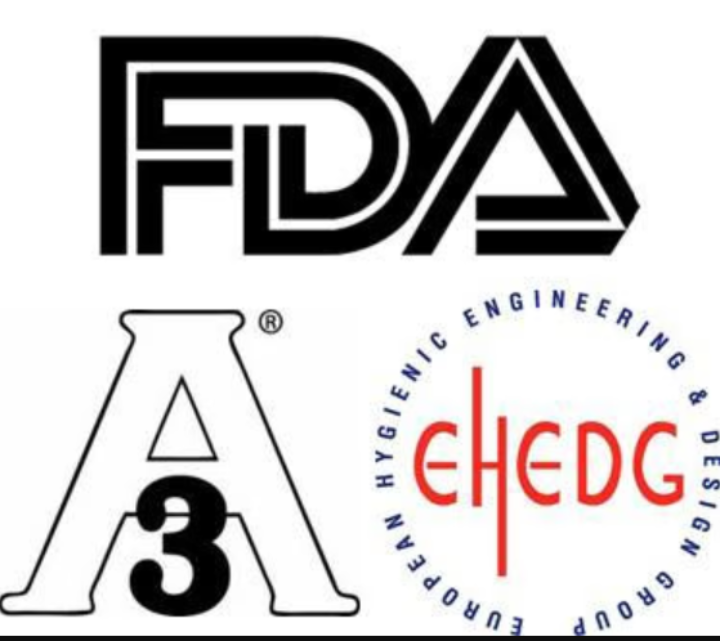
Contamination of Product
FDA regulations state that food contact surfaces need to be smooth, free of cracks and crevices, non-absorbent, cleanable, non-toxic and corrosion resistant to ensure that no food or bacteria can harbour and contaminate the product. 300-grade stainless steel is an example of an FDA approved material.
For more official compliance, pumps can be approved to 3A and EHEDG. These standards lay out criteria for the design and fabrication of equipment that comes into contact with food, which is then the third party evaluated. Whilst there are currently no legal requirements to use a pump officially certified by a third party and FDA is enough, a manufacturer’s duty to uphold public sanitary conditions mean many still opt for this
Could a new pump save you time, money and effort?
To find out how you can you can make your process more efficient and save on costly downtime and pump maintenance, speak to us today.