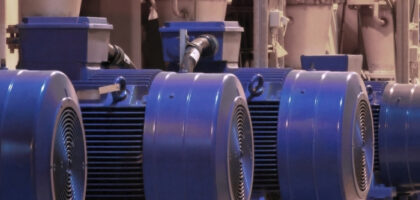
Self-Priming vs Submersible Pumps
Submersible pumps are frequently used to extract water from inside tanks or from rivers but what is it about submersible pumps that makes them chosen - what are the other options when repeated failure occurs or when flammable liquids need transferring? Should you contemplate using an ATEX submersible pump?
Submersible pumps are designed for pumping with the motor and pump both immersed in the liquid, and control of the pump is activated by float switches and typically submerged into a tank or pit.
True self priming pumps however, are surface mounted pumps which draw water from below (typically up to 8M) without the need for a non-return valve. They are kept outside the liquid, and can either be exposed to the elements or within a structure such as a pump house, and driven electrically, hydraulically or via an engine.
Usually, a submersible pump is the easy option and requires the least amount of engineering, but there are many advantages to using a self-priming pump over a submersible pump, and these can be split into three categories – maintenance, design features and liquid handling, but why choose a self-priming pump over a submersible pump?
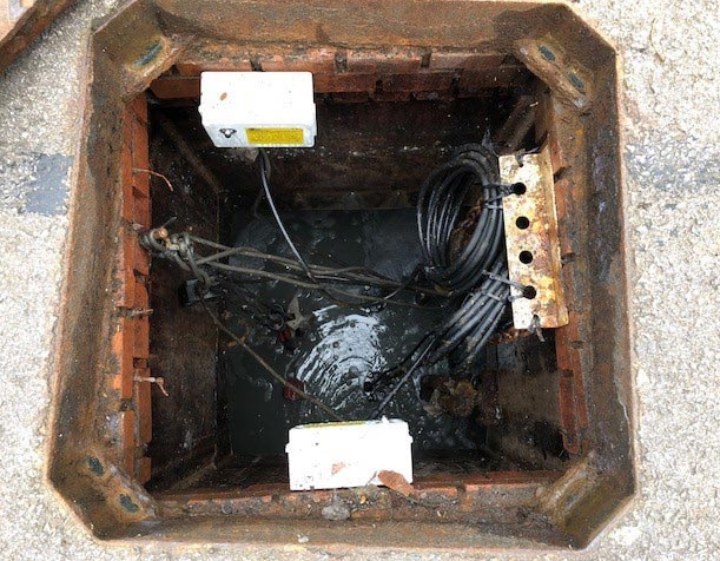
What liquids should be handled by self-priming pumps?
Submersible pumps are unsuitable for fluids like fuels, solvents, chemicals or other flammable liquids; one reason is because they could ignite when heated, and the other is because should they enter into the motor of a submersible pump, the liquids may not be chemically compatible with the pump casing, inner parts and cable glands. ATEX submersible pumps are increasingly being discontinued and for good reason! Self-priming pumps are a much better solution, given that should a seal fail in a submersible pump, ignition can occur.
Usually, a submersible pump will be kept cool by the fluid it’s immersed in, but as a result, the liquid around the pump motor heats up potentially causing an issue. Over time the cable glands on the motor will wear and the liquid will penetrate, eventually causing voltage leakage and the motor to trip. With a self-priming pump however, the number of different parts in contact with the fluid is far less, and should oil contamination occur in the fluid being pumped, it is generally only a small issue should it arise without your understanding. Furthermore, with submersible pumps, this can result in the cable gland becoming brittle, or swelling and leaking can occur which will cause the complete pump to fail.
Any submersible pump which is located at the bottom of any pit can be subject to grit ingress and quite often a submersible pump in a silty environment will be tied to a suspended bar above the pit to prevent it from becoming clogged with silt. By using a self-priming pump though, only the inlet pipe needs to be immersed into the fluid without additional chains or ropes, which can corrode over time.
Self-priming pumps can be used for more viscous liquids such as oils, creams, chemicals, and other foodstuffs but a submersible pump isn’t practical for pumping these types of fluid.
In sewage applications wet wipes, which are not designed to be flushed, are a huge issue for submersible pumps and typically stop the impeller from rotating as the wipes don't break up easily; this causes the majority of premature failures and are a hassle to remove. With a self-priming pump however, wet wipes can be pumped and do not cause an issue – but if a blockage does occur, then maintenance is far easier on a surface mounted pump than a submersed one.
How does maintenance compare?
As submersible pumps are fitted in pits they are not easily visible and usually the first sign of an issue is when the pump stops working. It’s at this point that the fault is then investigated, requiring a confined space entry team before the pump can be removed, involves several people, oxygen and is a costly exercise with the potential for long periods of downtime. Even if the pumps are mounted on to guide rails or chains, these can corrode over time meaning entry is required to resolve.
Service intervals on submersible pumps tend to be more frequent due to the complete unit being immersed in the liquid. Cable gland entry points need to be checked and replaced after five years as the rubber can wear and/or shrink on the cable glands leading to ingress. Also due to their nature of being ‘out of sight out of mind’, they can be neglected if a maintenance schedule is not put in place.
With a surface mounted self-priming pump there are various signals which can indicate maintenance is required such as signs of seal leakage, and if bearings are wearing there will be an audible noise. Suction and pressure gauges can be mounted onto the pump to ensure the pump is operating on the curve. As the pump is not submerged in the liquid they are also not subject to as harsh conditions, in particular in areas where freezing may occur such as in water abstraction from Canals, lakes or rivers.
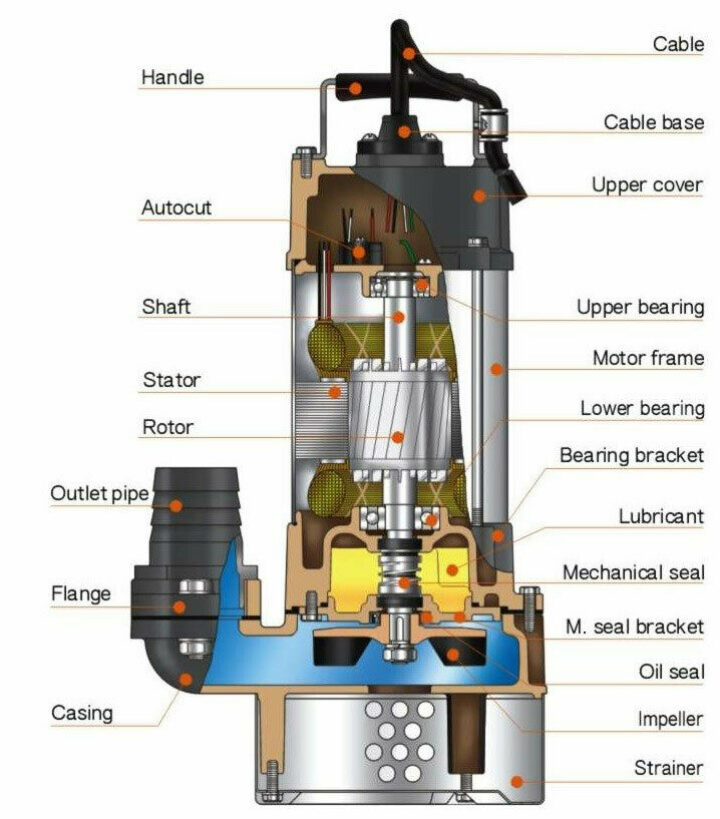
What are the design differences?
The design features of self-priming pumps offer additional peace of mind to customers. These pumps can last up to 20 years through their design, whereas a submersible pump will typically last up to five before heavy overhaul or maintenance is required.
Self-priming pumps are fitted with wear rings to optimise efficiency, and are of heavy duty design with an additional bearing so that they don’t solely rely on the bearing of the motor. There are separate shafts within self-priming pumps for the pump head and motor, ensuring that should the shaft or motor need replacing, these can be done so without the complete unit needing to be replaced too. Having twin shafts is a far more durable design as the load is shared between two shafts.
Furthermore, in a self-priming pump should the seal wear or fail, the liquid will not directly enter the motor, whereas on a submersible pump, this can cause the complete unit to fail. Submersible pump motors are usually immersed in oil and should the mechanical seal fail the oil will also contaminate the fluid being pumped. To repair the motor on a submersible pump after water ingress has occurred, it typically involves rewinding the motor, replacing the oil and possibly the capacitor too - meaning it may be more cost effective to replace the entire pump.
The motors on self-priming pumps are separate to the pump ensuring ease of replacement, but in the majority of submersible pumps the complete unit requires disassembling. Furthermore a self-priming pump can be maintained without disconnecting the pump from the pipework and is a far more robust solution.
Sometimes a submersible pump is specified due to low NPSH conditions, however a self-priming side channel pump can accommodate an NPSH as low as 0.5M for tank emptying or where liquids have a low vapour pressure and are in a sealed tank.
The Deciding Word
Although a self-priming pump initially has a larger outlay and requires additional engineering in order to accommodate the pump and suction pipework, it is a more robust, long term engineered solution and is economical during its lifetime. Typically during the lifetime of an application, a submersible pump will be replaced four times more than a self-priming pump. Therefore, we would recommend a self-priming pump be fitted as opposed to a submersible pump. Another alternative to a submersible pump is an immersed pump, whereby the motor is kept out of the fluid making it a more robust design compared to that of a submersible pump.
There are several types of self-priming pumps that we can specify depending upon the application. Some can handle entrained gases, be suitable for dry running and be seal less, but considerations also need to be given to the fluid being pumped.
We do not recommend submersible pumps to be used in ATEX environments and would select a more appropriate self-priming or immersed pump with a motor outside the fluid being pumped.
Does a self-priming pump sound like what you need?
If hearing the benefits over a submersible pump has convinced you, then take a look at our full range of self priming centrifugal pumps!