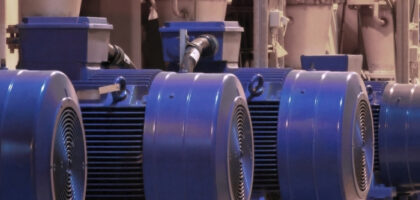
Pump Term Glossary
A 27 Term Glossary to Get You Through Sourcing a Pump
When sourcing a pump, it can be quite easy to get lost with all the technical jargon. NPSH, flooded suction, pressure loss… not necessarily phrases everyone uses day to day. Whilst some of the terminology may be general “engineers’ language”, other terms are much more specific to pumps, and if you don’t live and breathe pumps then you could understandably get confused.
Here we guide you through 27 terms that you’re sure to come across when buying or running a pump. Save this page to your favourites and avoid being baffled by pump lingo again…
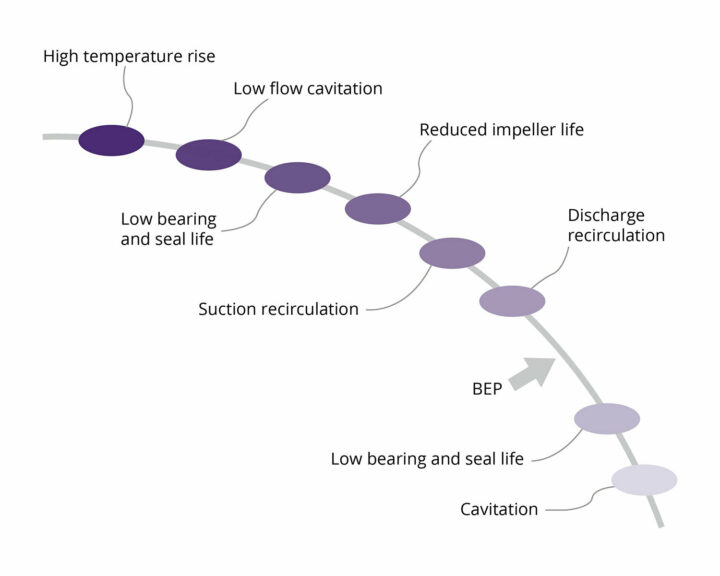
Back Pull Out
Where the motor can be removed without disconnecting the pump from the pipework for ease of maintenance.
Best Efficiency Point (BEP)
The point on a pump’s curve at which head and flow produce the greatest amount of output for the least amount of energy. Although a pump can operate anywhere on its curve, it does not mean it is efficient to do so.
Read more on how to read a pump curve and find the BEP here.
Cavitation
The process where a pumped liquid falls below its vapour pressure, causing cavities or bubbles to form. These cavities can collapse as they pass through the pump causing noise, damage to the pump’s internals and loss of efficiency. It is caused when NPSHa < NPSHr.
Centrifugal
The most common type of pump design. A centrifugal pump uses one or more impellers which attach to and rotate with the shaft, transferring the kinetic energy of the motor to the liquid, that then moves the liquid through the pump to the discharge point.
Read more about centrifugal pumps here.
Close Coupled
Where the pump head and motor are on the same shaft. Close coupled pumps benefit from a compact, cost effective design, but are less preferable for heavy duty, continuous use as there is more strain put on the common bearings and the size of the motor is usually limited.
Dry Running
When a pump is operated without fluid running through. This can result on overheating, cavitation and damage to internal parts such as impellers, casing, seals and bearings.
End Suction
Where the suction (inlet) of the pump is at one end and the discharge (outlet) is at the top of the casing, rather than being inline with one another.
Flooded Suction
Where the liquid source is held above the pump, allowing the suction chamber to be continuously filled through gravity and preventing any ingress of air. This type of installation means that the pump always remains primed, as long as the fluid source remains at an acceptable level.
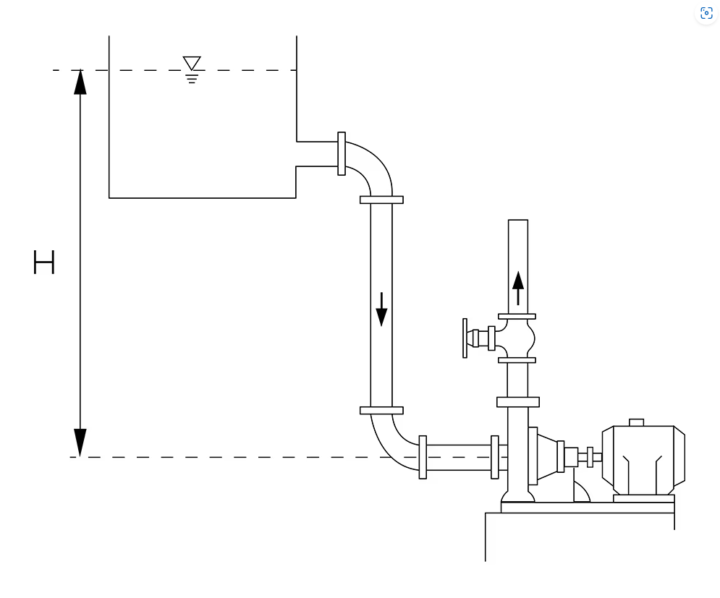
Flow Rate
The measurement of the liquid volume capacity of a pump, or in layman’s terms, how quickly the fluid is pumped. This is usually measured in litres per minute (l/min) or metres cubed an hour (m³h).
Friction Loss
The total head losses as the liquid flows from suction to discharge. Anything introduced within a fluid’s path will cause it to lose energy such as bends, valves or pipework. The more viscous a liquid, the quicker it will lose energy, and the more energy it will require to keep moving.
Read how to calculate a system’s pressure loss here.
Head
The amount of energy stored in the fluid due to the pressure applied to it, measured as a length/height of fluid, usually in metres.
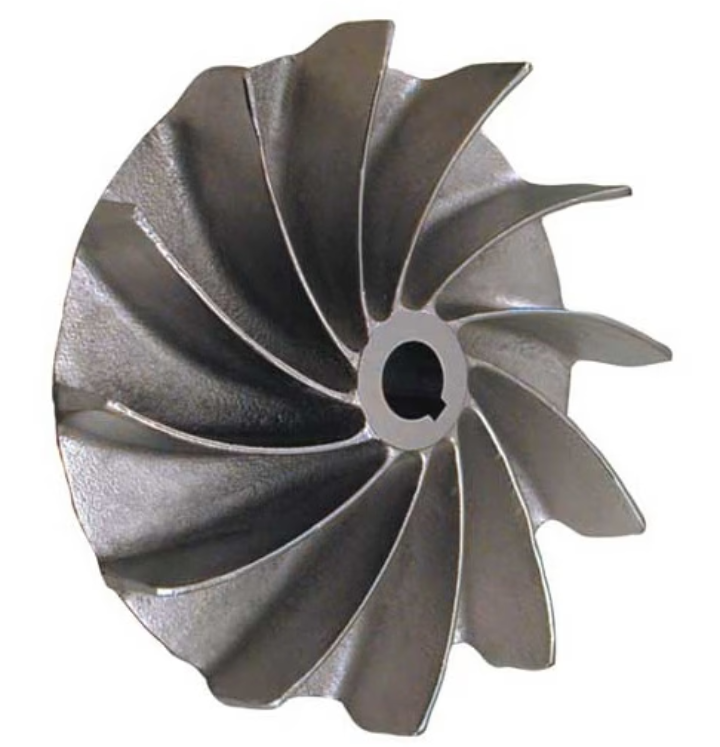
Impeller
The part of the pump that attaches to the rotating shaft and transfers kinetic energy to the fluid. The impeller diameter impacts the flow and head produced and can be trimmed to suit. Open impellers enable the handling of soft particles, closed impellers are for high efficiency and volatile fluids, vortex impellers can cope with stringy solids and debris and cutter impellers break down large solids.
Inline
Where the suction (inlet) and discharge (outlet) of the pump run in a straight line, rather than there being a change of pipeline direction like an end suction.
Long Coupled
Where the pump and motor are mounted on their own shafts, which are separated by a coupling. Long coupled pumps are usually more robust and suited to continuous use, as the separate bearings share the strain of operation and the space from the pump head protects the motor from seal leaks.
Magnetic Drive / Coupling
Where the motor is coupled to the pump not via a mechanical shaft, but via a magnet. The seal-less design of magnetic drive pumps reduces the change of leakages, making it ideal for the handling of aggressive fluids.
Multistage
Where a centrifugal pump has two or more impellers, as opposed to the one impeller of a single stage pump. Multistage pumps have higher pressure capabilities than single stage centrifugal pumps.
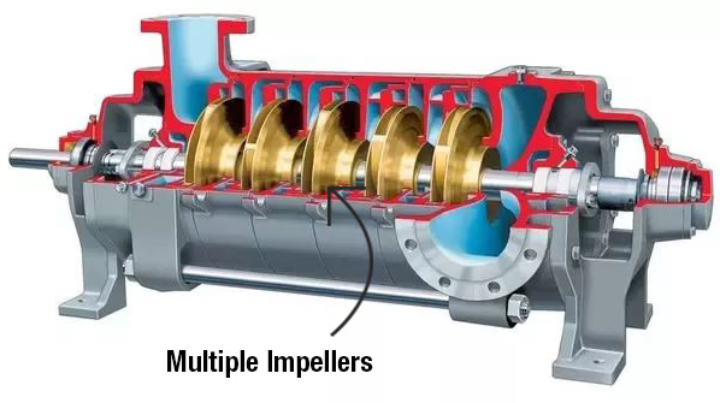
Net Positive Suction Head (NPSH)
NPSHr is the minimum amount of inlet pressure required to prevent cavitation, whereas NPSHa is how much is actually provided by the system. If NPSHa doesn’t meet NPSHr, then NPSHr can be lowered by reducing the speed of the pump, raising the fluid level nearer the pump or operating the pump close to its Best Efficiency Point.
Positive Displacement
A broad group of pumps made up of many individual working principles. Positive displacement pumps are categorised by an operation that moves fluid by trapping a fixed volume, usually in a cavity, and then forces that trapped fluid into the discharge pipe.
Read more about positive displacement pumps here.
Self-Priming
Where a pump placed above or inline with the fluid source is capable of evacuating the air within the suction line and creating a vacuum to draw in the liquid. Most positive displacement pumps are naturally self-priming, whereas centrifugal pumps usually require an additional priming pump fitted.
Shear
Stress or force applied to the fluid by the pump’s operation. Shear sensitive mediums are those that change in structure or viscosity when shear is applied such as creams, which get thicker, or honey, which gets thinner. These fluids should be handled by positive displacement pumps that apply low shear to keep them in as tact as possible, rather than centrifugal pumps which apply more shear.
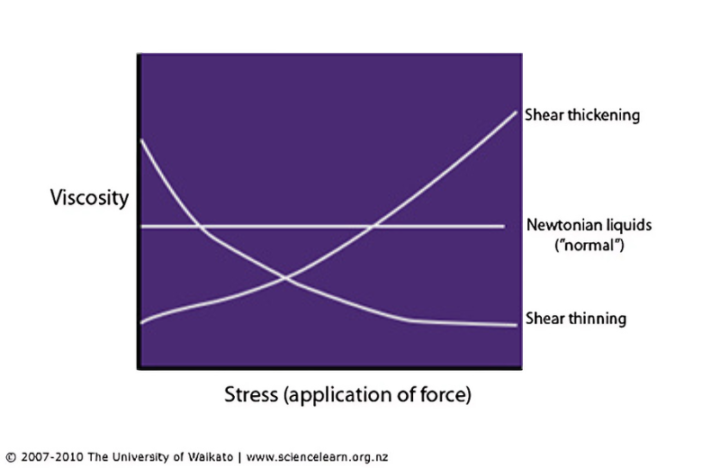
Single Stage
Where a centrifugal pump has only one impeller, rather than two or more like a multistage pump. Single stage centrifugal pumps tend to have higher flow, lower pressure capabilities than multistage pumps.
Split Casing
Where the double suction impeller or two single suction impellers of a centrifugal pump are supported between bearings, splitting the pump case into two separate chambers. Split casing pumps are capable of higher flow rates than other centrifugal pumps.
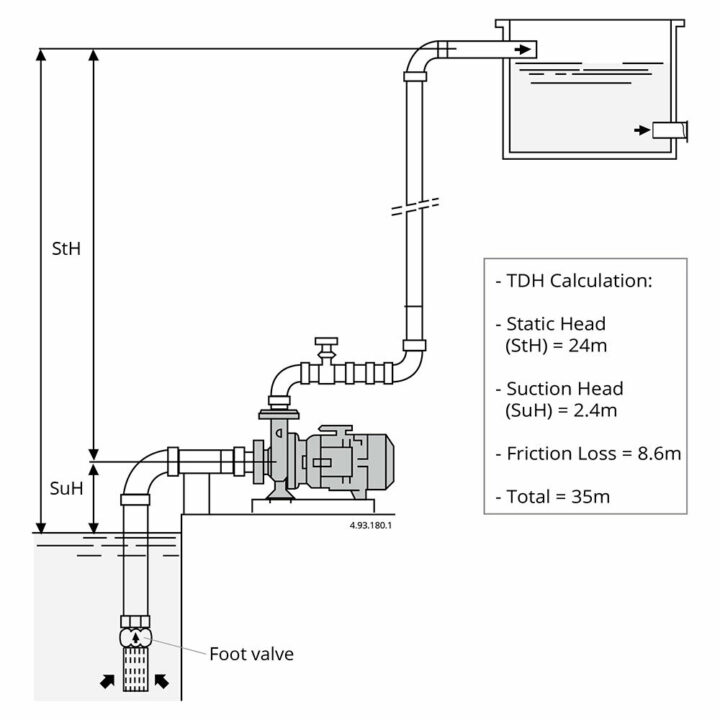
Static/Discharge Head
The head against which the pump must work when the liquid is stationary. It is essentially the height difference between the pump and the point of discharge, and should be noted at its maximum.
Suction Head
The difference in height between the fluid and inlet of the pump, when the source is above the pump. This should be noted as when the fluid in the container is at its highest.
Suction Lift
The difference in height between the fluid and inlet of the pump, when the source is below the pump. This should be noted as when the fluid in the container is at its lowest. This is sometimes still refereed to as Suction Head.
Total Dynamic Head
The sum of static head, suction lift and friction loss. It is essentially the system resistance that a pump must overcome i.e. what head it needs to work at to move the fluid through to discharge.
Need help choosing the RIGHT pump?
Our technical sales engineers are available to talk through your process requirements and specify the model you need.