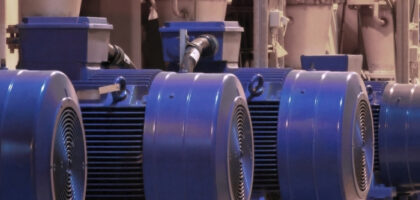
Pump Ordering Guide

The most important piece of advice when sourcing a pump is to make sure you are buying the right pump. This is obvious right? However a pump that works isn't necessarily the right pump - a pump may be suitable for an application, but if the installation is pushing the performance capabilities of the selected model, not only will it be operating less efficiently but the lifespan may be reduced.
With a vast range of pump types, material options and performance specifications, sourcing a pump requires experienced technical knowledge. Some procurers know exactly the pump they want, some know the performance requirements and others may solely know the application for which they need a pump. When you are unsure of exactly the pump you require, Castle Pumps understand that you need to be able to rely on an experienced supplier who can take the information you have and specify a solution that precisely meets the requirements.
This guide talks through the information we typically require to specify the best suited and most efficient pump for your application. You may not know the answer to every single point, but the more information you can provide us with, the better!
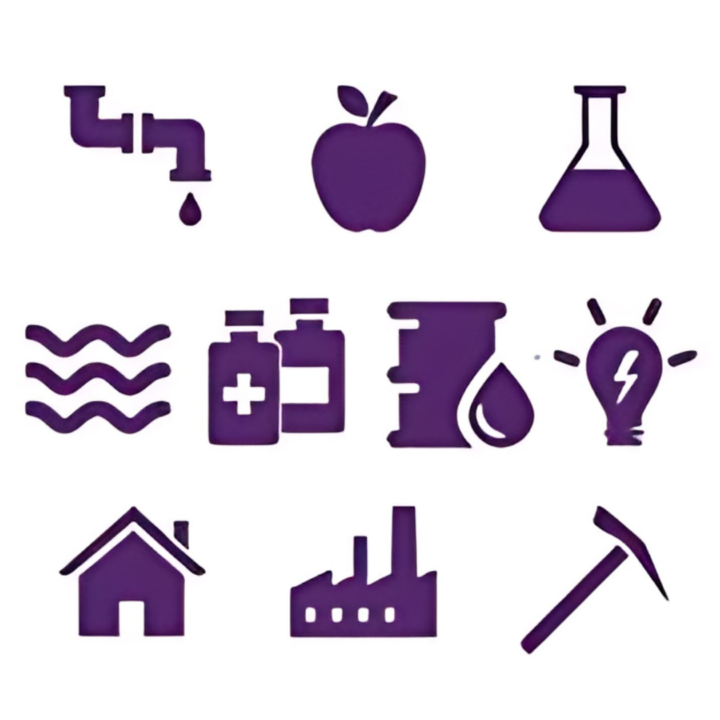
Application
The first place to start in the pump selection process is what exactly the pump will be doing. The more detail that the application can be described in, the better informed the decision will be as to selected material, design features as well as the rpm of motor.
For example, a pump that is for a continuous application will typically be specified with a larger motor run at a slower speed to reduce wear, have additional bearings and preferably be a easier to maintain in situ such as a back pull out design. Whereas if the pump is part of a production line that is run intermittently, a small motor run at full speed is more suitable, control features that reduce manual operation may be required and it’s likely to need to be self-priming to keep it unaffected by process stops and pauses in the line.
The environment the pump is being run in is also important as this can influence the need for certain approvals and certifications e.g. food grade, marine type approval or ATEX for potentially explosive atmospheres.
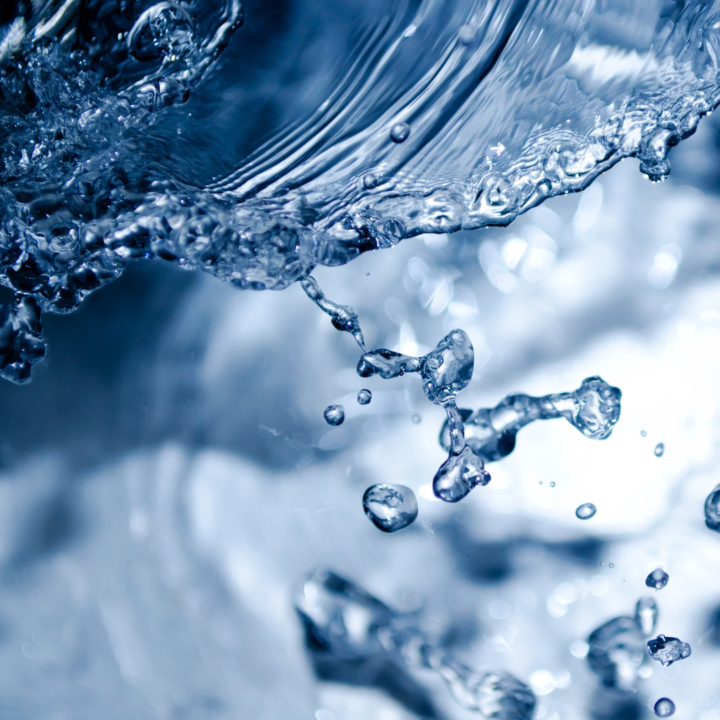
Fluid
Full disclosure of the liquid is needed to ensure its compatibility with the pump wetted parts, including the casing, impeller, wear rings and any elastomers fitted. The fluid will therefore have a direct influence over the materials selected. Typically, cast iron is used for fresh water and fuels, and bronze for seawater. We have a complete fluid/material compatibility guide available here.
The fluid not only affects the materials but also the pump type selected. For example, whilst centrifugal pumps work excellently with water, screw pumps and gear pumps are better suited for lubricating fluids such as fuels and oils. The presence of solids or high viscosity sludges need pumps capable of handling high pressures and can pass particles such as peristaltic pumps or progressive cavity pumps.
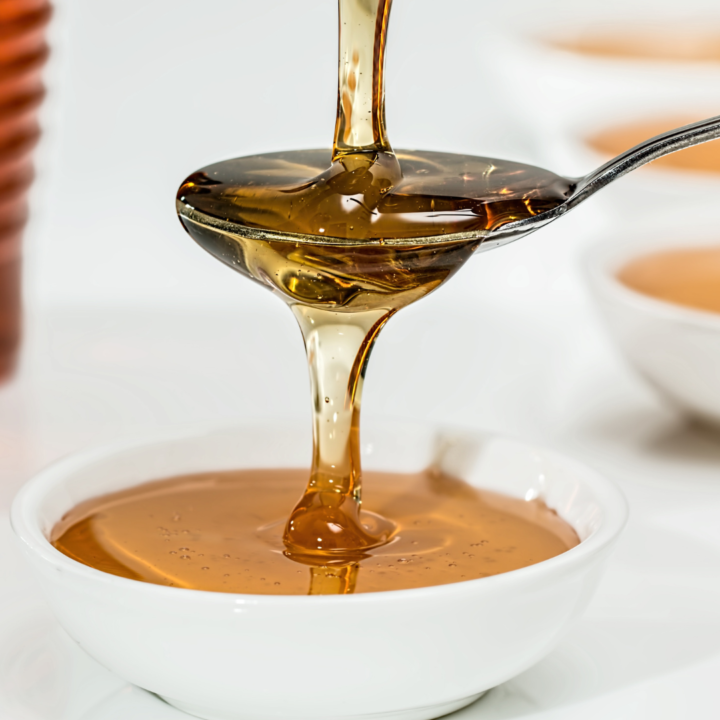
Viscosity
The viscosity and temperature may also be required to determine the power absorbed by the pump, as well as any impellers required to provide the specified duty. Some fluids’ viscosity can change depending upon temperature (butter gets thinner as it melts) or force (cream gets thicker as it’s whipped!). Let's take the example of Heavy Fuel Oil (HFO) to demonstrate the impact on the pump - as it gets colder, its viscosity increases a lot. At 20cSt, if a flow rate of 98M³H is desired at 2.5 bar, a 12Kw motor is required. To produce the same flow rate at a viscosity of 1500cSt, the pump for HFO will now require a motor of 28KW.
For shear sensitive fluids, those where force being applied changes their structure/viscosity, positive displacement pumps are usually selected as they apply low shear to keep the fluid in as tact as possible.
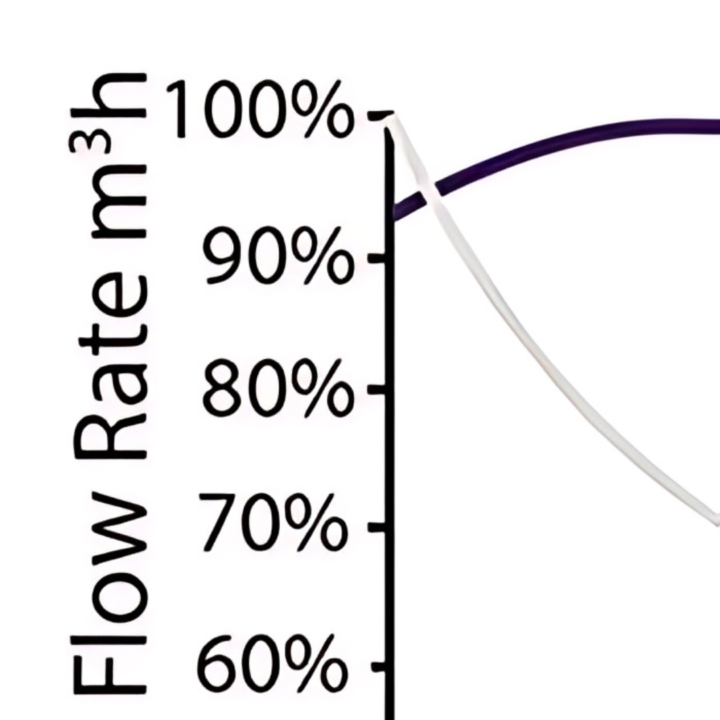
Flow Rate
Flow rate refers to the measurement of the liquid volume capacity of a pump, or in layman’s terms, how quickly the fluid is pumped. This is usually measured in litres per minute (l/min) or metres cubed an hour (m³h). This is an important factor in selecting the right pump, as the quicker the speed at which you need to transfer the fluid within your system, the higher the flow rate the pump needs to be capable of. On the flip side, if the pump needs to accurately dose small quantities of liquid as part of a production process, it needs to be able to cope with extremely low flow rates.
The required flow rate of the pump must be able to be achieved whilst also working at the pressure/head requirements of the system, which is why a pump's performance curve is so critical in pump selection.
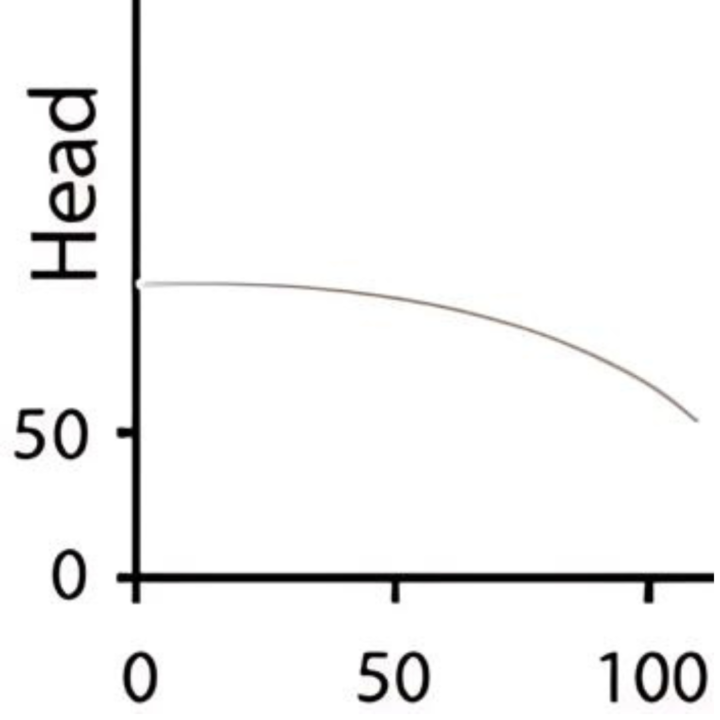
Pressure/Head
Consideration also needs to be given to the pressure, usually measured in bar or metres, that the pump needs to work at to move the fluid the required distance. This needs to take into account the suction lift and discharge head of the system, as well as any friction losses within the pipework. Certain pump types are capable of much higher pressures than others. For example, when it comes to centrifugal pumps, at certain pressures a multistage pump may be required over a standard single stage pump.
Just like what we said with flow rate, the required head of the pump must be able to be achieved whilst working at the flow rate requirements of the system i.e. a point on the pump's performance curve.
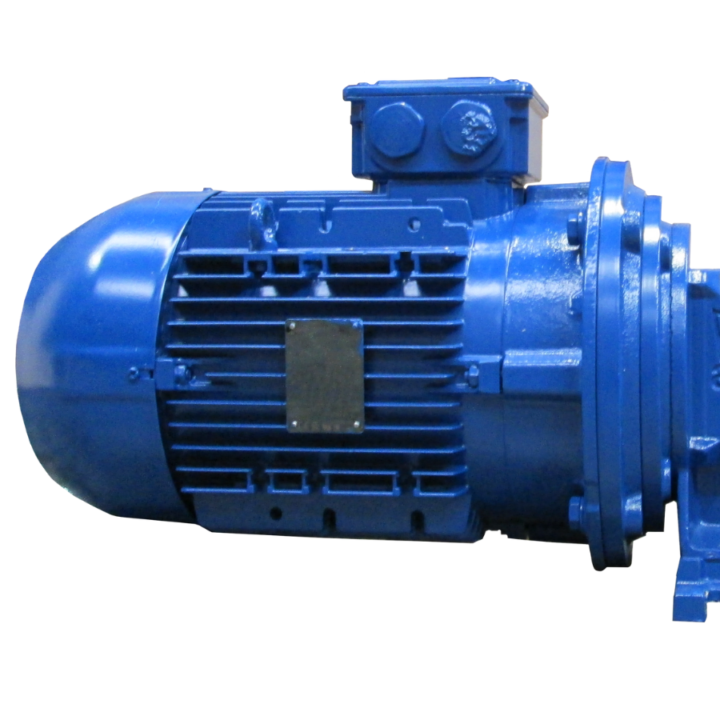
Voltage & Frequency
The power available on site for the pump to run off is a big point to consider – sites, or vessels if we are talking marine applications, may be operating on either single or three phase. It is important that this information is made clear at the outset. As well as voltage, frequency is important to think about. A pump being run at 60Hz produces 20% more flow and pressure than the same pump in 50Hz, which shows how depending upon the frequency of the motor, different pumps could be specified for identical applications.
In some instances, voltage and frequency may be irrelevant. For example, often in industrial processes air operated pumps are a better suited alternative to an electric powered motor.
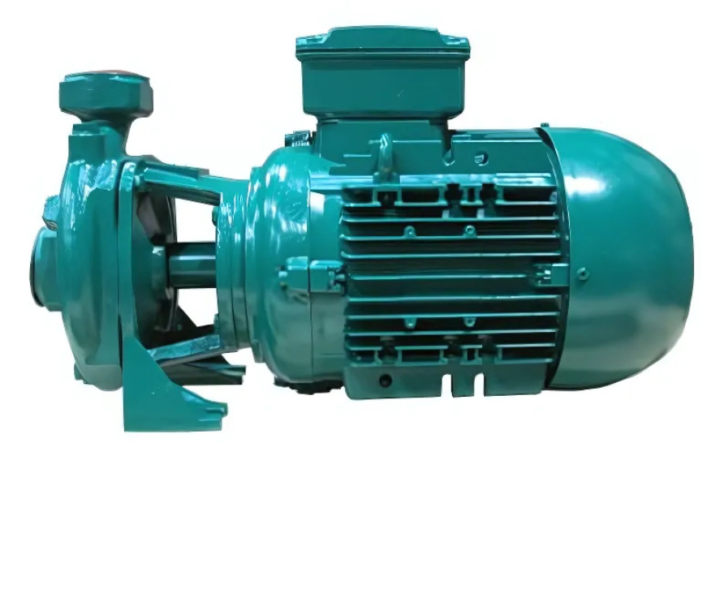
Suction Conditions
What suction conditions the pump is under in an installation has a huge influence on the pump selection process. A flooded suction is where the liquid source is held above the pump, continuously filling the suction chamber through gravity, preventing any ingress of air and ensuring the pump remains primed. In situations where it is not possible to keep the suction flooded, a self-priming pump must be used. Most positive displacement pumps are naturally self-priming, whereas if a centrifugal pump is selected, it will usually require an additional priming pump to be fitted.
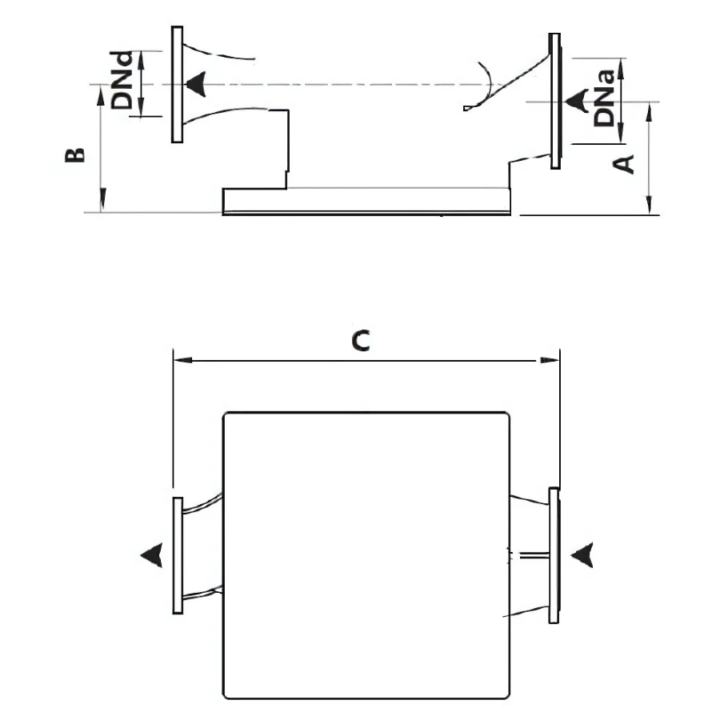
Dimensions & Orientation
If there are any specific dimensions or existing pipework requirements for an installation, this will also help determine the pumping solution most suitable. For example, if space is an issue a vertical pump may be more suitable than a horizontal orientated option. The way the pipework of a system is planned may also require the pump’s inlet and outlet to be in a certain configuration i.e. vertical inline, bottom suction or end suction.
If an existing pump needs replacing, the replacement may need to be specific dimensions to fit within the pipework. Some manufactures construct models to match existing pump and pipework specifications, and DIN 24255 pumps are also available that can be interchanged with other DIN 24255 pumps.
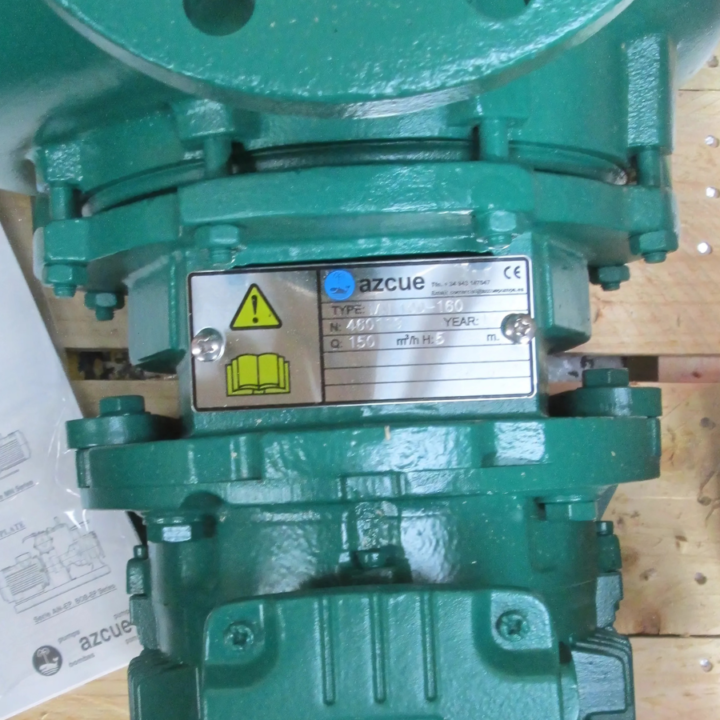
Replacing an Existing Pump?
Pumps can be manufactured to a variety of specifications including wetted part material choices, mechanical seal, motor size, frequency, rpm and any additional accessories. The serial number is therefore essential to guarantee an exact replacement is supplied, as the model number alone may not indicate the unique pump specification. The serial number is usually indicated below the pump model on the name plate and on some pumps also engraved on the discharge flange
Have you got a pump enquiry?
Fill out our pump specification form to the best of your knowledge and send to sales@castlepump.com for us to specify a pump that meets your requirements.