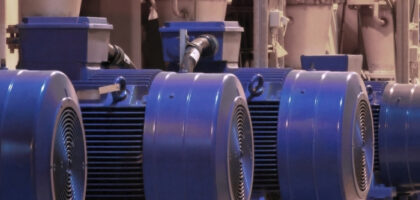
Pump Couplings – A Comparison of Rigid, Flexible & Magnetic
What Is a Pump Coupling?
A pump coupling is the element used to connect the rotating pump shaft to the drive shaft of the motor; enabling the motor to efficiently transmit power to the pump.
When a pump is close coupled, a separate coupling is not required as the motor is directly mounted to the pump on a single shaft. Whilst close coupled pumps benefit from a compact, cost effective design, they are less preferable for heavy duty, high power, continuous use as there is more strain put on the common bearings and the size of the motor is usually limited.
For heavier duty applications, long coupled pumps are more suited. As the pump and motor are mounted on their own shafts separated by a coupling, the separate bearings share the strain of operation, therefore extending the lifespan of the mechanical parts.
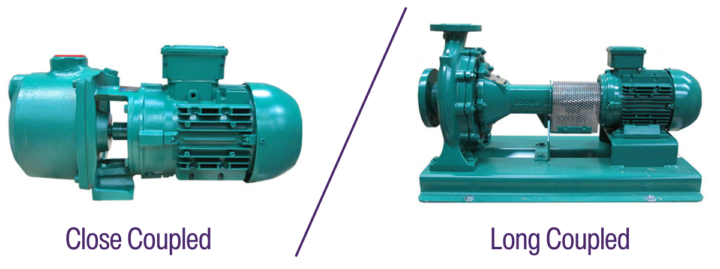
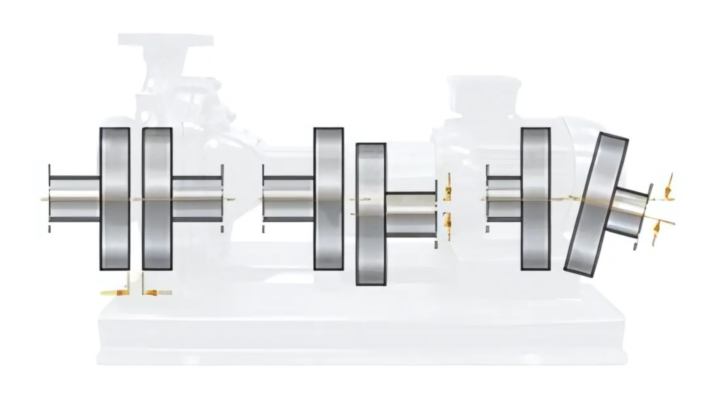
The Issue of Misalignment
The coupling of the two shafts would be simple if they remained perfectly aligned and there were no vibrations during operation. However, in reality this isn’t the case, and any misalignment can result in the premature wear and failure of the bearings, mechanical seals and even the coupling itself.
Misalignment is when one or both shafts are forced from its desired position, of which there are three main types:
- Axial – Where the shafts are parallel but either too close or too far apart
- Radial – When one shaft is positioned higher than the other.
- Angular – Where the two shafts are positioned at different angles to one another.
The problem of misalignment is one of the factors that need to be considered when the coupling is selected, as the different types cope with it differently. So, what are the different types of pump coupling and when should they be used?
The 3 Types of Pump Coupling
Rigid couplings
As their name suggests, rigid couplings connect the pump and motor shafts together very firmly, which allows them to transmit more power to the pump than flexible couplings of a comparable size. They also benefit from a simpler, more cost-effective design. However, rigid couplings don’t have the ability to handle any shaft misalignment without high stress on the bearings and seals as are unable to absorb any vibrations from the pump running, or thermal expansion. They are usually used for applications where misalignment is not a concern, for example where the shafts have been precisely positioned in perfect lateral and angular alignment at installation.
Flexible Couplings
Unlike rigid couplings, flexible couplings can accommodate some movement e.g. vibrations and thermal expansion without damage. This makes them ideal for applications where there is a degree of unavoidable misalignment between the drive and pump shafts. As they can absorb vibrations well, they can also be used to reduce excessive operating noise. With these benefits come a more complex, expensive design. However, as flexible couplings protect the shaft and bearings from damage and premature wear, there are maintenance savings to be had in the long run.
Magnetic Couplings
Magnetic couplings differ to rigid and flexible as rather than a mechanical shaft, the motor is coupled to the pump by a magnet which offers various benefits. Firstly, with magnetically coupled pumps there is a small air gap between the magnet and the motor and pump. As there is no physical contact, misalignment and thermal expansion is not a problem. The absence of a mechanical seal also eliminates the chance of leakages, making a magnetic drive pump ideal for handling aggressive or hazardous fluids.
However, magnetic couplings are only suited to clean liquids as the presence of any particles can be problematic as they stick to the magnet. They are also sensitive to extreme operating conditions; if excessive torque exceeds the capabilities of a magnetic coupling, the magnetics may decouple, and the pump shaft will slip causing stoppages. Therefore, when selecting a magnetic coupling, you need to be sure that is aligned with the power of the system.
Summary Comparison
Rigid | Flexible | Magnetic | |
---|---|---|---|
![]() | ![]() | ||
Type | Mechanical | Mechanical | Non-Mechanical |
Torque Transmission | Higher due to firm connection | Lower than a comparable rigid coupling | Can decouple under extremely high torque |
Misalignment | Not suitable for installations where misalignment is present | Can accommodate a certain degree of misalignment in the system | Absence of physical contact means it isn’t a problem |
Vibration / Thermal Expansion | Unable to absorb | Able to absorb | Absence of physical contact means it isn’t a problem |
Cost | Lower | Higher | Higher |
Wear | Wears overtime and needs replacing to prevent leaks | Wears overtime and needs replacing to prevent leaks | Wearing of the coupling itself is not a problem |
Have you got a pump enquiry?
Our technical sales engineers are available to talk through your process requirements and specify the model you need.