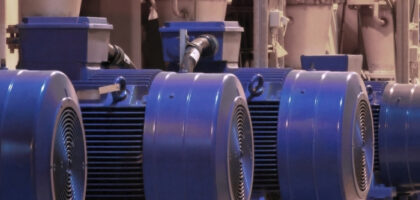
The Importance of Considering a Pump’s Total Life Cycle Cost
When it comes to sourcing pumps, or indeed any equipment, businesses are increasingly faced with budgetary pressures that can see them making purchasing decisions that are not the most economical in the long term. This is usually the case when the buyer considers only the upfront costs of the purchase, rather than the total Life Cycle Costs.
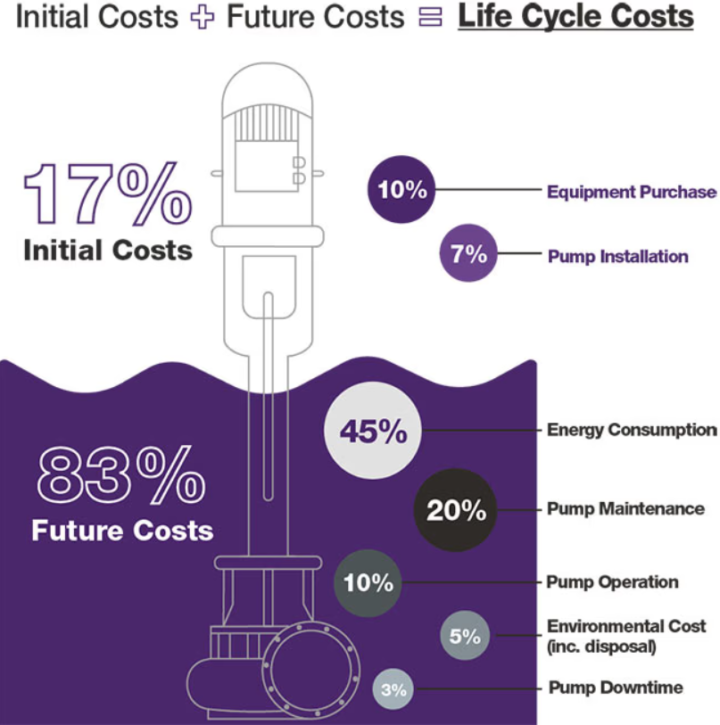
What are Life Cycle Costs (LCC)?
The concept of Product Life Cycle Costing was first adopted in the 1960s by the US Department of Defense to aid military procurement decisions. The basic principle is that by considering all costs associated with buying, operating and maintaining products, the lowest long term costs will be achieved:
LCC = Initial Costs + Future Costs
Initial Costs of a Pump
The initial or upfront costs are those that are most easily identifiable at the point of purchase. These include the price of the pump to buy, plus delivery and any installation costs required. Typically, these are the costs that procurement teams consider.
However, some upfront costs can also be overlooked. One example is the initial training that the pump operators or engineers may need at the point of installation. This is a cost that should be considered at pump purchase, as some pumps may require more manual intervention in their operation than others and therefore more training. Or perhaps your operators have been using a pump for many years and know how to operate it. Would buying a very slightly cheaper pump that works completely differently warrant the training costs?
Future Costs of a Pump
Putting a monetary value on future costs can be difficult, which is possibly why many choose to neglect to even see them as part of the total cost of buying a pump or piece of equipment. The problem is though, that for a typical installation, future costs can amount to around 83% of a pump’s life cycle costs, and initial costs only the remaining 17% (World Pumps, 2017). This is itself enough to demonstrate the importance of considering the other costs associated with running and maintaining the pump over its lifetime.
Labour – Labour is the biggest overhead in almost all companies and therefore wasted time is wasted money. If the pump you’re considering requires its operators to manually intervene a lot, then this an additional cost you need to consider. A pump supplied with certain automation or control features such as preset batch meters or level switches may initially be more expensive, but the time it saves your workers could be huge.
Energy – According to the US Department of Energy, 16% of a typical industrial facility’s electricity costs are generated by pumps. Methods of reducing the energy consumption of your pump include installing a variable speed drive to operate the motor at actual requirements, investing in parallel pumping systems so that a large pump doesn’t have to be run when duty requirements can vary greatly and installing certain control features to ensure a pump doesn’t operate for any longer than necessary. Whilst all of these ultimately add to the initial costs of the pump, the impact on future costs can be huge.
- Maintenance - Like any piece of mechanical equipment, all pumps will need routine maintenance as parts wear. By carrying out regular servicing, not only do you extend the lifespan of the pump, but you are less likely to incur unexpected failures and downtime. The manufacturer’s instruction manual will advise as to the frequency of routine maintenance such as visual checks. They will also recommend to replace certain components such as the mechanical seals, wear rings and impellers every 1-2 years to prevent leaking and other issues. The costs of carrying out this routine maintenance however can depend upon pump specific factors such as the complexity of servicing, the price of spare parts and the quality of the pump’s internal components. Let’s say you are choosing between two pumps. You have a centrifugal pump cast in bronze that benefits from a back pull-out design, which means that the motor and pump internals can be removed without disconnecting the pump from the pipework. The other option is a couple of hundred pounds cheaper, but it is made of pressed metal, which being thinner is more susceptible to damage and misalignment when knocked and needs to be removed from the installation whenever maintenance is required. Yes, the initial costs of the latter are cheaper, but over the lifespan of the pump, will maintenance costs exceed the difference?
Downtime – Depending upon the pump’s application, downtime can be extremely costly for a business in terms of loss of output or alternative costs. Imagine your pump plays a critical role in your production line; it is responsible for dosing a specific quantity of ingredient into a mix. If the pump unexpectedly fails, then the production of the mix comes to a halt. The cost of this downtime could be the loss of revenue, the unhappy customers whose demand you haven’t met or the labour costs of an employee having to take over manually. Where downtime costs are unacceptably higher, when purchasing a pump, you need to consider a backup pump in a parallel pumping system that kicks in when the other fails, as well as the availability of spare parts to ensure maintenance can be carried out quickly. If for example, you need to wait for delivery from another country, then keeping spares on-site is the answer.
- Disposal - Generally speaking, this cost shouldn’t vary too much across pump types, with one exception – if the pump handles hazardous fluids. If hazardous fluids are handled than during decommissioning, the pump will need to be thoroughly cleaned out for environmental purposes. A “clean in place” or self-cleaning pump would therefore save time and effort here.
Need help choosing the RIGHT pump?
Our technical sales engineers are available to talk through your process requirements and specify the model you need.