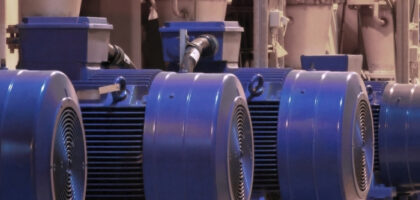
Automating Your Pump to Reduce Manual Operation
“Wasted time is worse than wasted money” is how the quote goes, but in fact, wasted time IS wasted money for your business. Labour costs are one of the most expensive overheads in any company. So, when you think of your existing processes, are you spending more time than necessary on the operation of your pumps? However, freeing up your workers’ time for more value-adding tasks isn’t the only reason automating your pumps is important. It can also prevent pump damage, improve accuracy and reduce waste. Below are ways that you can automate your pump, or download our handy infographic here.
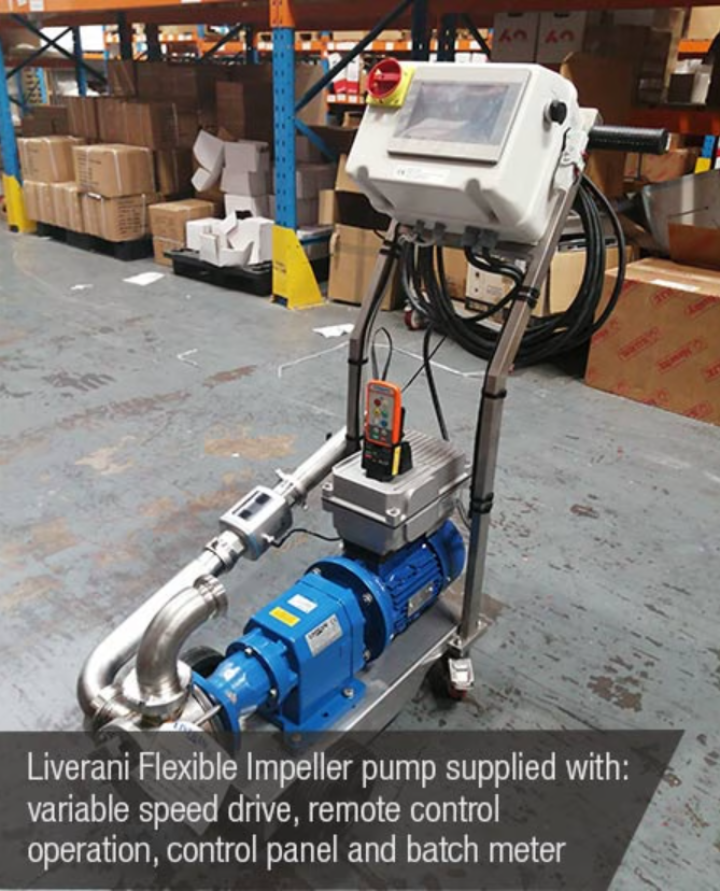
1. Pump Timer
Sometimes you may wish the pump to start and run for specified periods of time and then stop. For example, a circulating application may need a fluid to be pumped for 10 minutes every 4 hours around a tank to prevent it from sitting still for too long and the ingredients separating. By fitting a timer, this would not only reduce the amount of time spend by someone walking to the pump and operating it, but it also eliminates the chance of someone forgetting and it not being done.
2. Batch Meter
Pumps that are responsible for dosing or transferring a specific volume of fluid can be supplied with a batch meter that can turn the pump off once the amount is reached. Not only does this reduce reliance on the operator, but it also ensures the amount is accurate and easily repeated. Batch meters are ideal for container filling applications and for adding a set amount of fluid/ingredient into a mixture.
3. Stroke Counter
A stroke counter is similar in principle to a batch meter for air operated pumps. It counts the amount of times air is ejected by the pump and can turn it off once a specified number has been performed. By knowing how much fluid is transferred per stroke, you can use it for batching. It should be noted, however, that if the viscosity of the fluid can differ, it will be inaccurate.

4. Level/Float Switches
Level switches can also control the pump start/stop cycle. When the fluid in a container has reached a certain level, the pump will turn on or off and continue until the sensor detects the other specified level. The use of this form of pump automation is popular for tank emptying and filling and dewatering applications.
5. Dry Run Protection
If a pump is left to run with no fluid passing through it, then it can overheat, cause component seizure and damage to the seals and impellers. Pauses in your production line or your operators forgetting to turn the pump off can result in dry running. Some pump designs such as AODD or peristaltic pumps can dry run without damage, but if using a pump that doesn’t such as a centrifugal pump, then a dry run sensor can automatically turn the pump off when it is detectedл
6. Leak Sensor
The fitting of a leak sensor can turn a pump off upon detection of fluid leaking from the pump. These are good practice, particularly for pumps handling high-cost product or hazardous fluids and chemicals that can be dangerous or flammable if in contact with.
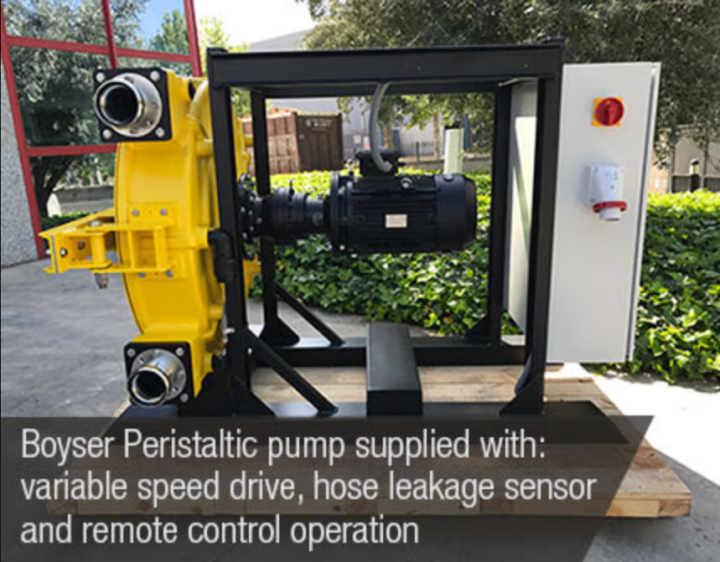
7. Variable Speed Drive
Where there are differing duty demands on the pump at different times, VSDs can help automate the speed of the motor to actual requirements rather than maximum capacity. They can be used to slow down or speed up the pump’s motor depending upon the pressure detected in the system.
8. Remote Monitoring
Sophisticated remote monitoring systems have integrated data loggers that can monitor things like vibrations, pressure and motor current to ensure that issues can be spotted in advance without an engineer having to always manually attend the pump to inspect it.
9. Remote Control
Some pumps can be supplied with a radio operated control pad to enable pump start/stop or reverse operation to be carried out without having to walk over to the pump. If a pump is operated multiple times per day, productivity can be drastically improved by removing this requirement.
Start saving with pump automation features!
If you're suffering from wasted engineer time, inefficiency or product waste, discuss your process with our pump experts who will find you a solution.