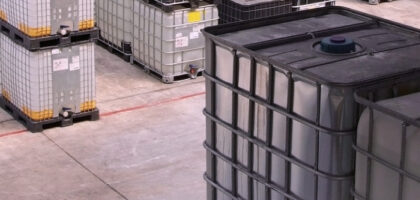
Chemical Industry Pumps
The right chemical pump starts with chemical compatibility but doesn’t end there!
The right chemical pump starts with chemical compatibility but doesn’t end there!
If you’re dealing with chemicals, you’ll likely understand that failure to get a pump compatible with your chemicals can result in corrosion, swelling, dissolving or brittleness and ultimately it is leaking and failing. We give special considerations to the materials we specify, considering not only the chemical but the temperature and concentration. For example, Hastelloy C is compatible with Hydrochloric acid at 10% at 20°C, but at 40°C it has limited resistance.
Whether it’s a chemical dosing pump you need for accurate metering, a chemical drum pump for barrel emptying or one for tank to tank transfer, Castle Pumps are likely to have solved your requirement before for another client.
Where Our Chemical Pumps Are Used
With thousands of different chemicals and solutions being used throughout almost every industry and manufacturing process, there are unlimited requirements for our wide range of chemical pumps. Common applications we solve include:
- Cleaning solutions and detergents
- Acids and solvents
- Fertilisers and pesticides
- Pickling in metal surface finishing
- Leaching in the mining industry
- Water treatment & pH adjustment
- Process and manufacturing fluids
- Paints, inks, bleaches and dyes
- Resins and adhesives
Benefits of Our Chemical Transfer Pumps
So, what makes our pumps for the chemical industry ideal for use in their applications:
- Chemical metering pumps for highly accurate dosing of chemicals even at the lowest of flow rates
- Control features to help productivity such as variable speed, dry run protection, level switches and batch meters!
- Chemical barrel pumps with 99.98% emptying capabilities to prevent waste of product at the bottom of the container
- Magnetic drive pumps coupled without the presence of mechanical seals to limit the chance of leaking hazardous fluid
- ATEX approved models for the safe handling of flammable chemicals or fluids in a potentially explosive environment
- Wide material selection to ensure chemical compatibility and prevent premature failure and wear
- Plastic and stainless steel models to allow for a range of budgets
Who We've Worked With in the Chemical Industry
Case Studies
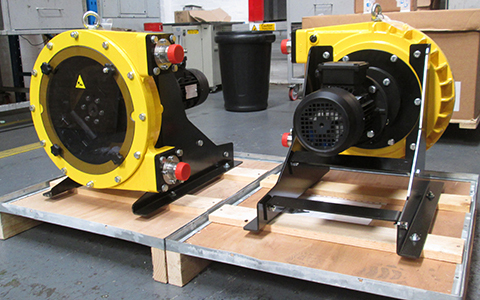
Tank to Tank Transfer for Chemical Manufacturer - Peristaltic Pumps
On certain occasions, the required specifications don't make for a difficult selection. This company needed a pump suitable for chemicals, to be transferred from tank to tank with a low flow rate. Our selection was based upon the capabilities of the pump in question, and it's ability to slow down the flow rate to the desired range. This customer was very happy with our suggestion and placed the order for the exact pump within two days of their initial enquiry.
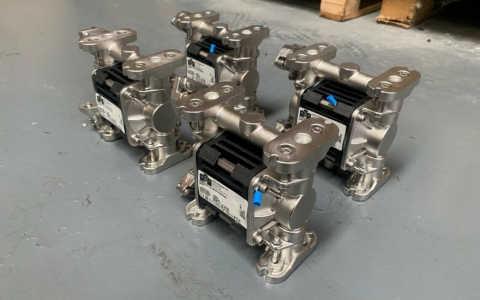
Solvents for Metal Reclamation – AODD Pumps
Castle Pumps were approached by a precious metal reclamation and recycling company looking for a number of the same pumps. They wanted a solution for transferring the solvents used for the cleaning of recycled metal product surfaces to be used in the pharmaceutical industry. The requirements of the pumps included being driven by air as opposed to an electric motor due to previous pumps used and being capable of offering a good service life despite the aggressive nature of the solvents.
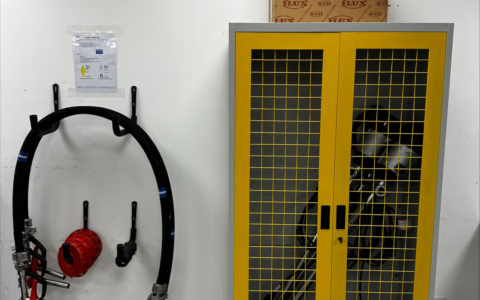
Vape Flavour Dispensing from IBCs - Food Grade Barrel Pump
Castle Pumps received an enquiry from a manufacturer of vape liquids and flavours who were looking to upscale their production. Part of this involved improving the efficiency of transferring the concentrated flavours from the IBCs where they are stored. The customer was looking for a number of container emptying solutions for fitting onto the IBCs and dispensing the favours without manually handling the fluid. They were looking for a number of container emptying solutions for fitting onto IBCs.