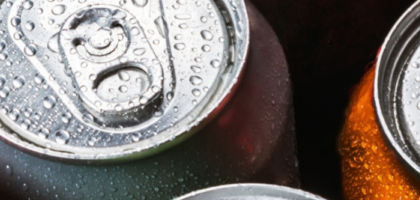
Ready to Drink Cocktail Producer – Flexible Impeller Pumps
Case Study Information
- Customer: Ready to Drink Cocktail Producer
- Pump: Liverani EP MIDEX Flexible Impeller Pump
- Application: Ready to Drink Cocktail Production
- Industry: Food & Drink
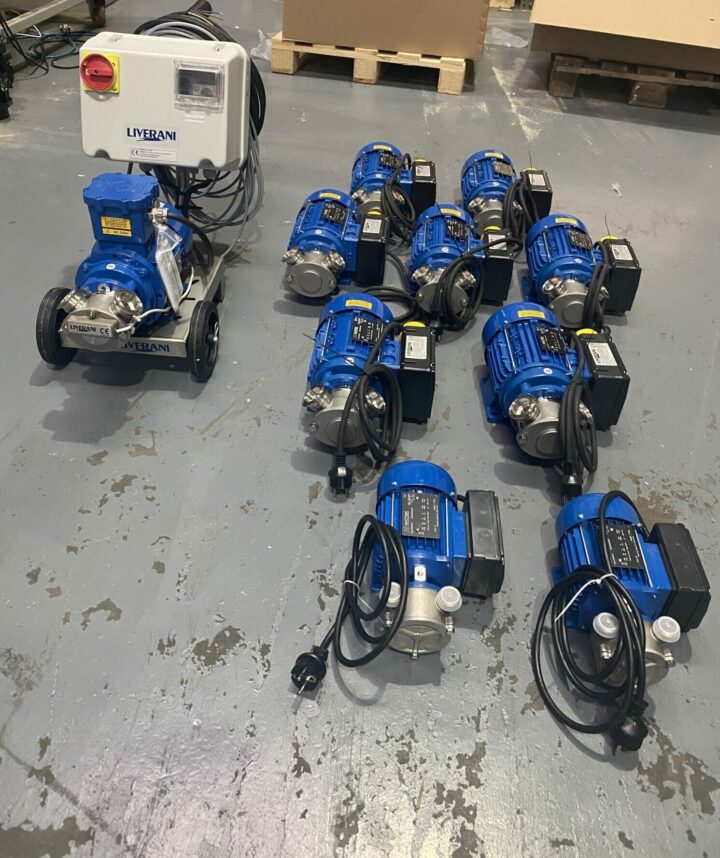
Enquiry
We were approached by a manufacturer of ready to drink cocktails looking for pumps for the transfer of various fluids used within the recipes, as well as the finished product. The initial enquiry was just for two pumps, which they wanted to trial to see if it was worth upgrading all of their existing alcohol transfer pumps on site used for handling their drink products.
After 6 months of excellent service, they returned with an enquiry for another 7 of the same distillery pumps plus another pump for transferring 55% proof alcohol, and two for handling cleaning solutions as part of their canning machines’ Clean in Place system.
Key challenges:
Shear sensitivity of the alcohol products
The flammable nature of the 55% proof alcohol
Food grade approvals required
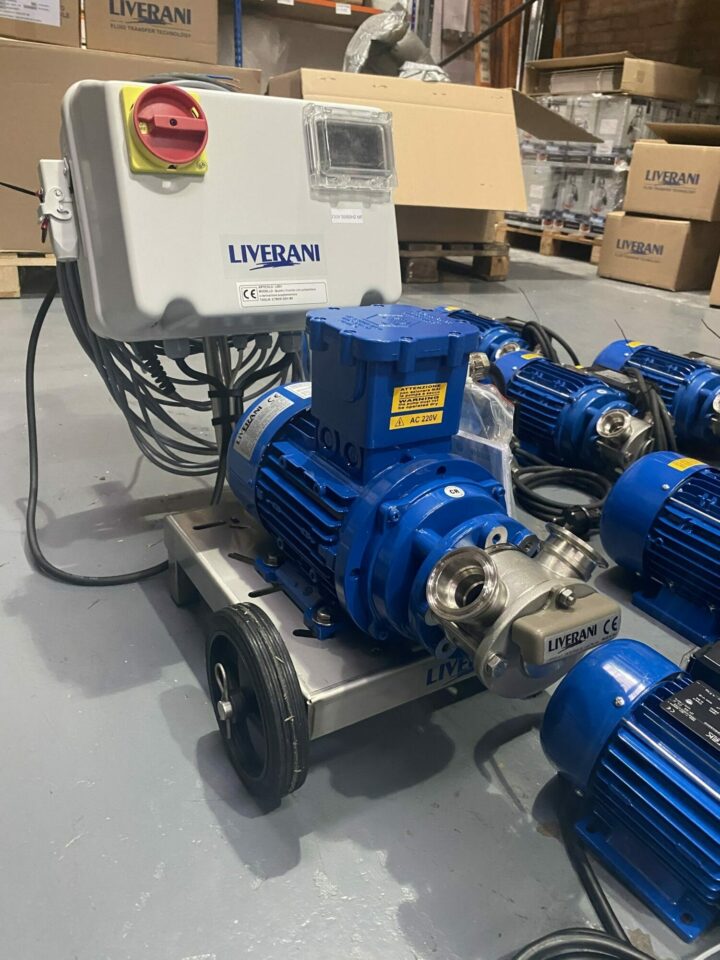
Solution
Equipment Supplied:
Model: 7 x Liverani EP Midex Flexible Impeller Pumps
- Fluid: Cocktail mixture
- Impeller: Neoprene Food Grade
- Fittings: 1 ½” Triclover
Model: 1 x Liverani INV Midex Flexible Impeller Pump
- Fluid: 55% proof alcohol
- Impeller: Neoprene Food Grade
- Fittings: 1 ½” Triclover
- Mounting: Trolley
- Drive: Inverter with dry run protection
- ATEX motor
Model: 2 x Liverani Liquid Ring Pump
- Fluid: Cleaning chemicals
- ¾” BSP
When it comes to alcohol transfer, flexible impeller pumps are our go to pump design. Firstly, they are a common cost-effective solution for food transfer applications where the fluid is relatively easy to handle. We specified these food safe pumps with a food grade Neoprene impeller, compatible with the alcohol products and Tri-clover connections that meet ISO 2852 standards for hygienic couplings.
Secondly when it comes to the handling of drink products, it is often important that the pump applies low shear during the transfer process, which the flexible impeller design does. This is because the agitation of the product can lead to frothing and the impact on taste.
For the pump required to pump the 55% proof alcohol there were some additional requirements. The first point we recognised was that we needed to supply it with an ATEX motor due to the flammable nature of the fluid. In addition we provided dry run protection to prevent any overheating to further the limit of sparks in the environment.
The customer also told us that this alcohol transfer pump would be transported around the manufacturing plant to pump from various containers. Based upon this, we suggested it to be trolley mounted for increased portability, and supplied with an inverter to allow it to be run at different speeds when transferring different quantities from different tanks.
Do you need a distillery pump to upscale your production?
If you want to reduce manual operation and bottle, fills barrels or transfer your product quicker, all whilst maintaining the taste you’ve worked so hard on, we can help you!