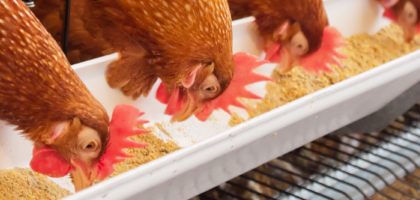
Abrasive Waste at Chicken Factory - Vertical Immersion Pump & Vortex Impeller
Case Study Information
- Customer: Chicken factory
- Pump: Azcue VRX Vortex Impeller Vertical Immersion Pump
- Application: Chicken waste
- Industry: Food & Drink
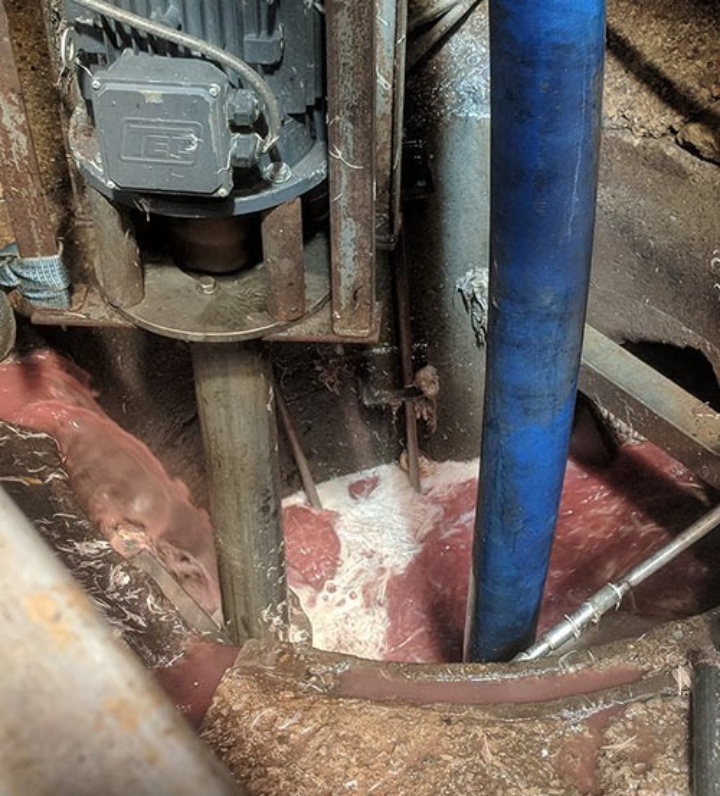
Enquiry
Castle Pumps received an enquiry from a new customer in the UK, a halal chicken factory who were having problems with their existing vertical immersion pump from another supplier. The pump was being used for the transfer of a sludgy chicken waste including blood, feathers and water from a container, and due to this abrasive solid content, it was often clogging multiple times a day.
With the abrasive fluid pump regularly going down, the production line was continuously coming to a halt resulting in large amounts of downtime and manual intervention from the employees on site. As the pump was vital to the operation of the factor, the failure of the pump was resulting in large scale costs in both labour and loss of output.
Key Challenges:
Able to handle the abrasive solid content
Provide a non-clog solution
Needed to fit into an existing installation
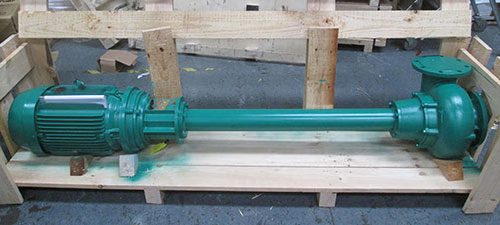
Solution
Equipment Supplied
Model: Azcue VRX Vertical Immersion Pump c/w Vortex Non Clogging Impeller
- Application: Chicken waste transfer
- Installation: Vertical
- Pump Body: Cast Iron
- Impeller: Bronze
- Voltage: 400v
- Motor: WEG 22Kw 4 Pole IE3
We attended site to conduct a thorough evaluation of the application and site conditions leaving no stone unturned. This gave us as much information as possible to be able to make an informed decision on which pump was needed for the job.
As the current installation used a vertical immersion pump there was little room in the pipework, so we too specified this pump design that is able to immersed directly into the waste container. To allow the ease of passage of feathers, we oversized the pump giving as much margin for error, as at various points during the production, huge clumps could go through the pump with less fluid content than is ideally recommended for operation. The Azcue VRX vertical immersion pump we specified also comes with a vortex impeller, allowing the pump to create a vacuum so that large solids can pass through without interfering with the pump’s internals.
The customer received a set of in-depth instructions specifically tailored to the application to avoid at all costs the possibility of the pump clogging. The results of providing a pump suitable for the application and also providing expert technical assistance has allowed the factory to run for over 3 months (and counting) clog free. Previously the unit which was originally on site would only run for a maximum of 24 hours before a clog occurred.
Do you need a pump for an abrasive slurry?
When it comes to abrasive slurries, you need an anti-clog solution that will pass the solids or stringy content without downtime. That's where our solutions can help you.