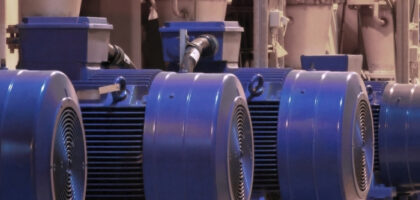
Anaerobic Digestion Plant
Case Study Information
- Industry: Energy & Fuel
Customer: Anaerobic Digestion Plant & Processing Facility
Location: UK
Equipment supplied
1 x PT-100/15 - Heavy Duty Peristaltic Pump
- Application: Organic Waste Sludge Pump w/ Abrasive Solids in Suspension (25-30%)
- Capacity: 30 m³/hr @ 3 Bar Max
- Required Suction Lift: 4-5 m
- Offered Suction Lift:
- Existing Pipe Size: 150 mm
- Max Viscosity: 8000 cPs
- Inlet / Outlet Connections: DN100 / PN16 Stainless Steel Flanges
- Geared Motor: 15 kW / 1500 rpm / 400-690V / 3 Phase / 50 Hz / IP55 / Class F
- Body, Wheel, Pressing Shoes: Ductile Cast Iron GGG40
- PT-100-VAC Air Operated Vacuum System
- 1 x 15 kW Variable Frequency Drive & Sinusoidal Wave Filter
- 1 x Customised Automatic Reversing function
Enquiry
An Anaerobic Digestion Plant and Processing Facility called Castle Pumps to assess the problems they were having with their existing immersible, progressive cavity, digestate transfer pump and installation, and could we recommend a suitable alternative and provide recommendations to optimise the installation to improve their efficiency.
The client was experiencing persistent problems with their existing pump clogging, running dry and failing to deliver the required capacities when at their heaviest solids load. Their pump would run for 3 minutes max before cutting out, drawing air and no fluid upon initial testing and commissioning. Furthermore, as their existing pump was an immersible pump, over 5 meters in length, the client was required to hire a crane to lift the pump out of its chamber to do any inspection, maintenance or repair work on the rotating assembly.
Solution
Further to Castle Pump’s initial site visit and report on their existing set-up, we recommended the customer replace their existing pump with a peristaltic pump. These Organic Waste Sludge Pumps have several unique features which were perfect in solving our client’s problems.
- They can run dry indefinitely, therefore eliminating any problems caused by blockages in the suction or delivery pipework.
- They are excellent at handling both water like substances as well as slurries, so they are perfect for digestate transfer.
- They can perform suction lifts of up to 9.8 m vertically, so we were able to fit the pump to the top of the tank and suck straight out of it, therefore avoiding the need to hire a crane during routine maintenance or repair.
- Their only wear part is the hose, so maintenance costs and down time are kept to a minimum.
- The pump can be run in both directions - a feature we cleverly used to our advantage by installing an automatic reversing function, which operates for 30 seconds before every start up to blast any blockages caused by the settlement of the suspended solids in between operating hours, in both the suction and delivery pipework.
By over sizing the pump we were able to reduce the running speed of the pump and therefore the wear on the hose, extending its life and reducing the maintenance costs. Furthermore, another advantage of over sizing the pump meant we could fit a variable frequency driven (VFD) to the unit, so the client could vary the flow rate to cater for both varying solids loads and increased production requirements.
Castle Pumps also provided the customer with:
Various 4" Suction & Delivery Hosing and Customised Fittings for PT-100/15 Peristaltic Pump
2 x 4" Expansion Bellows, Carbon Steel Flanges & EPDM Moulded Rubber Belows
1 x Multi-Flanged Wafer Pattern Butterfly Valve - EPDM Liner
- Size: 4" to fit PN6/10/16, ANSI 150, Table D & E Flanges
- Temperature Range: -10ºC to 120ºC
- Body: Epoxy Coated Ductile Iron
- Disc: Stainless Steel 316
- Liner: EPDM
- Shaft: Stainless Steel
- Washer: Galvanised Carbon Steel
- Circlip ISO 3075: Steel
- O-Ring: Viton
- Lever: Aluminium
- Bolts: Galvanised Carbon Steel
2 x Multi-Flanged Wafer Pattern Butterfly Valve - EPDM Liner
- Size: 6" to fit PN6/10/16, ANSI 150, Table D & E Flanges
- Temperature Range: -10ºC to 120ºC
- Body: Epoxy Coated Ductile Iron
- Disc: Stainless Steel 316
- Liner: EPDM
- Shaft: Stainless Steel
- Washer: Galvanised Carbon Steel
- Circlip ISO 3075: Steel
- O-Ring: Viton
- Lever: Aluminium
- Bolts: Galvanised Carbon Steel
You can download this case study by clicking on the image below...