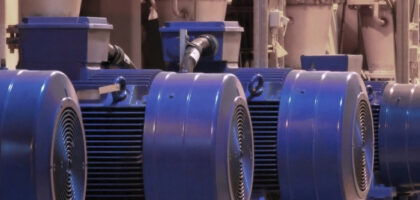
Side Channel Pump Guide
How do side channel pumps work?
Side channel pumps, or liquid ring pumps as they are otherwise known, are somewhat of a hybrid between a positive displacement pump and a centrifugal pump. Upon start up, a side channel pump begins to operate like a positive displacement pump as it self primes, but soon begins to act like a centrifugal pump once the side channels become filled with fluid.
The liquid is drawn in and enters the impeller blades and the side channel which is open at just one point in the casing, rather than the entire circumference, which is where the term liquid ring comes from. As the star shaped impeller rotates, the pumped fluid moves back and forth several times between the blades of the impeller and the side channel. This creates a strong transfer of energy and results in an increase in pressure up to 10 times greater than that of centrifugal pump rotating at the same speed.
Design benefits
High pressure generation - As discussed above, the working principle of side channel pumps generates pressures up to 10 times the pressure generated by other pump types operating at the same speed. This makes it suitable for high pressure applications including those where the fluid needs to be pumped across long distances or through small pipework. The casing is also designed to withstand high pressures, and often liquids such as LPG are stored in a pressurised container to keep it in liquid form as at atmospheric pressure it becomes a gas. Water can also be pumped at temperatures above boiling point (100°C) providing the water is kept pressurised above atmospheric pressure.
High entrained gas capabilities – Liquid ring pumps are able to handle gas and vapour content without any interruption to the fluid flow or damage caused to the internals due to dry running. They are therefore often the choice for pumping liquids with up to 50% gas content, as other pump types such as centrifugal pumps have a very limited capacity.
Excellent self-priming – Side channel pumps are able to generate a high suction vacuum making them self-priming. They are therefore a suitable solution for applications with difficult suction conditions such as the emptying of a fuel tank. As the fluid collects in the outer area of the side channel and impeller blades, a liquid ring forms to facilitate the self-priming process.
Low NPSH requirements – Thanks to its axial and large diameter suction side flow path there is little flow disturbance, meaning that side channel pumps benefit from low pump speeds and ultimately lower Net Positive Suction Head requirements compared to other, higher speed pump types. This means that the amount of inlet pressure required for the pump to operate efficiently is less than that of a standard centrifugal pump.
Low risk of cavitation –When a liquid drops below its vapour pressure, the liquid vaporises which can create holes in the pump casing causing leaking and a reduction in output efficiency; this is the process of cavitation. Thanks to their lower pump speed, lower NPSH and ability to handle gas content, liquid ring pumps are less vulnerable to cavitation at variable vapour pressures compared to other pump designs.
Typical applications of a side channel pump
Side channel pumps are ideal for low flow, high head applications involving low viscosity, clean fluids. Whilst suitable for a range of fluids from water to fuels to chemicals, because of the design’s narrow tolerances, liquid ring pumps are not suitable for abrasive particles and solids.
The design benefits of the liquid ring pump make it a popular solution for applications where standard centrifugal pumps fail. Firstly, they are excellent solutions for the handling of high temperature fluids such as in boiler feed applications and chemicals such as ammonia that is pumped at close to boiling point or where liquids are kept under pressure to keep them in a liquid form. They also able to cope with fluids containing up to 50% gas such as Liquid Petroleum Gas (LPG) and condensation.
Side channel pumps’ ability to self-prime combined with their low risk of cavitation makes them ideal for handling liquids near their vapour pressure safely and efficiently.
Applications that side channel pumps are typically used within include:
- Volatile liquid transfer
- Boiler feed
- LPG pumping
- Tank emptying
- Heating/air conditioning
- Condensation extraction
- Sea water transfer
- Reverse osmosis
- Hot water circulation
- Refrigerants
Does this sound like what you need?
If from reading the above it sounds as though a side channel pump is most suitable for your application at hand, take a look at our range of pumps.